Laser Welding Industry Solution
Laser welding is an advanced welding technology that combines modern and traditional techniques but has different characteristics than traditional arc welding. It has obvious advantages such as anti-electromagnetic interference, fine weld seam, narrow heat affected zone, beautiful and smooth welding surface, high welding strength, safe non-contact, no back-melting problem, and high processing accuracy.
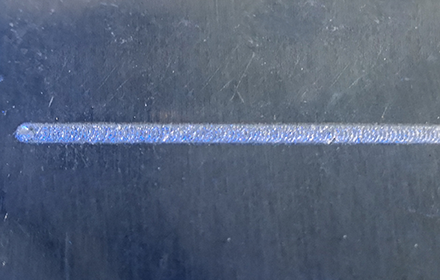
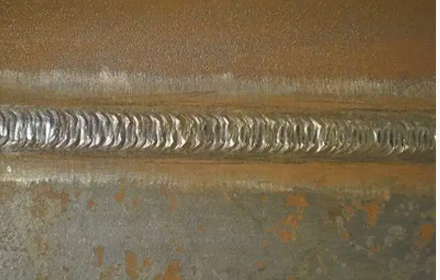
Here we quote the video from Vico.com to illustrate the advantages and development history of laser welding.
Affected by the high cost of equipment, laser welding has long been used only in automotive production, aerospace, and high-end manufacturing fields.
In recent years, due to major breakthroughs in domestic laser welding technology, equipment costs have been greatly reduced, and laser welding has been widely used in various industries. A large number of traditional welding scenarios, such as argon arc welding, are being replaced by laser welding.
In order to make laser welding more convenient and efficient for users and to promote the popularity of robot laser welding, the iNexBot control system has launched a special system for laser welding. With the iNexBot system, domestic robots can easily upgrade laser welding processes.
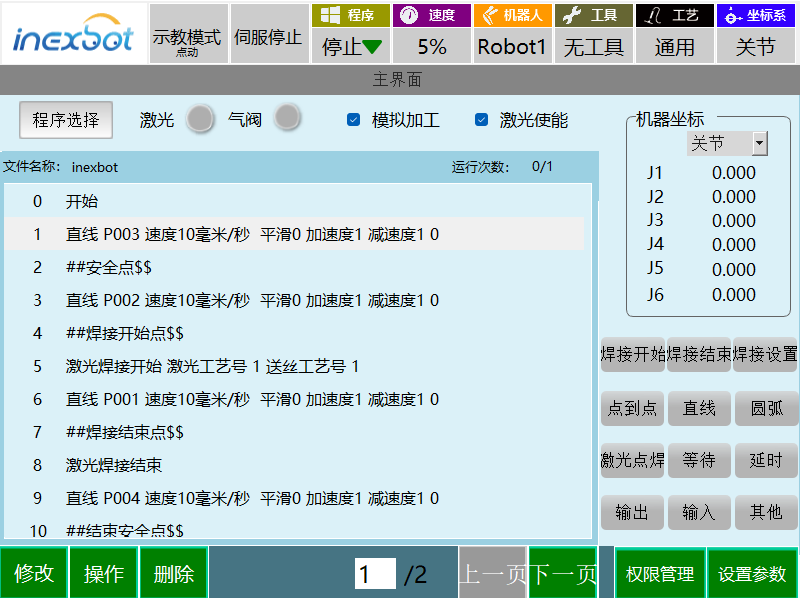
iNexBot laser welding system has its own PWM output, and does not require special PLCs and control equipments. Compared with traditional welding, it is simpler and more concise. Besides, dynamic power, intelligent wire feeding, and PWM high-speed pulse control functions are added to the previous laser welding, making the welding process smarter, faster and more stable.
System Features
Specialized instructions for laser welding
Traditional robot laser welding uses PLC for control, which inevitably requires a large amount of PLC programming and involves a large number of IO calls, making it extremely complex.
The iNexBot robot laser welding system is equipped with specialized laser welding instructions that completely replace PLC programming. It only requires a few simple lines of instructions to operate. At the same time, the interface has been fully optimized to facilitate users in quickly establishing programs. It also includes spot welding instructions for spot welding scenarios.
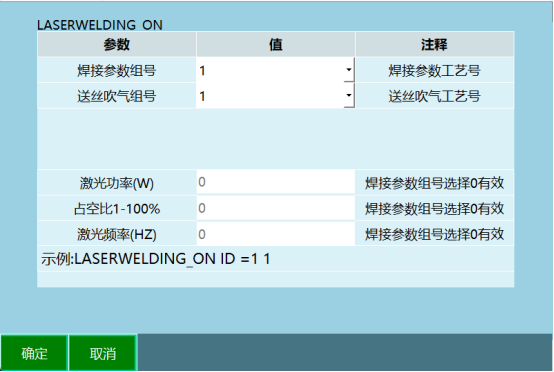
Expert parameters
After conducting extensive research on laser welding, iNexbot has summarized and extracted the expert parameters required for laser welding. These parameters were carefully designed and organized into a concise and efficient parameter interface. The parameters are simple and clear, enabling rapid deployment while also supporting high levels of customization for complex laser welding scenarios.
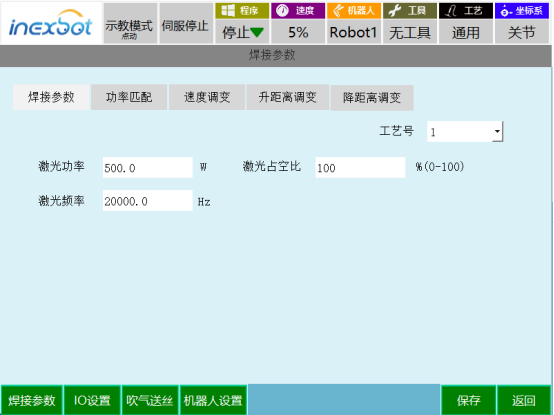
High-precision welding
Thanks to the dynamic motion control algorithm of the iNexBot control system, the robot can suppress vibration and maintain high precision while operating at high speed. This enables the full potential of high-speed and high-precision laser welding to be realized.
Dynamic laser power adjustment
Laser welding is prone to undercutting, where the weld does not fuse properly with the base metal, resulting in a groove. Temperature issues may also occur at the start and end of the weld, such as overheating at the end and insufficient temperature at the beginning. These problems are caused by poor matching of welding speed and power during the laser welding process. The iNexBot laser welding system has a built-in dynamic laser power adjustment function, which perfectly solves the above problems.
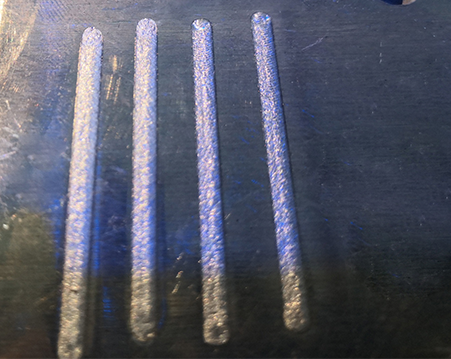
Dynamic wire feeding speed control
In some laser welding scenarios, there may be issues like thermal cracks (such as crystal cracks or liquation cracks). In such cases, filler welding is required to reduce or eliminate the cracks.
When using conventional wire feeders, once welding begins, the wire feeding speed becomes uncontrollable, which can easily cause weld buildup. Based on this, the iNexBot laser welding system has developed a real-time controllable wire feeding speed function to ensure the aesthetic appearance of the weld seam.
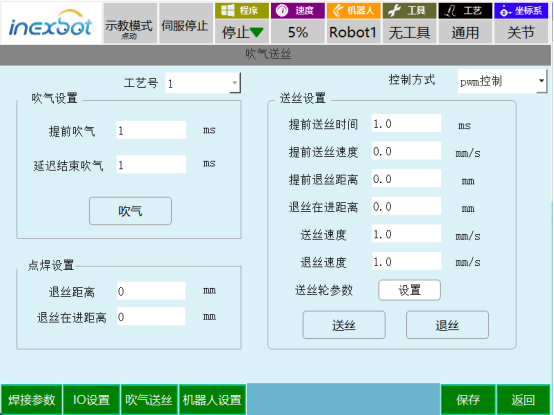
Fine power control
One major advantage of laser welding is that by adjusting the power, the surface temperature of the metal can be maintained near its boiling point, thus preventing metal spattering or pitting during welding.
The iNexBot laser welding system has a built-in dual control mode of analog signal and PWM (high speed pulse), which allows for high precision and fine control of laser power density on metal surfaces. It is easy to adjust the laser precision for different base materials.
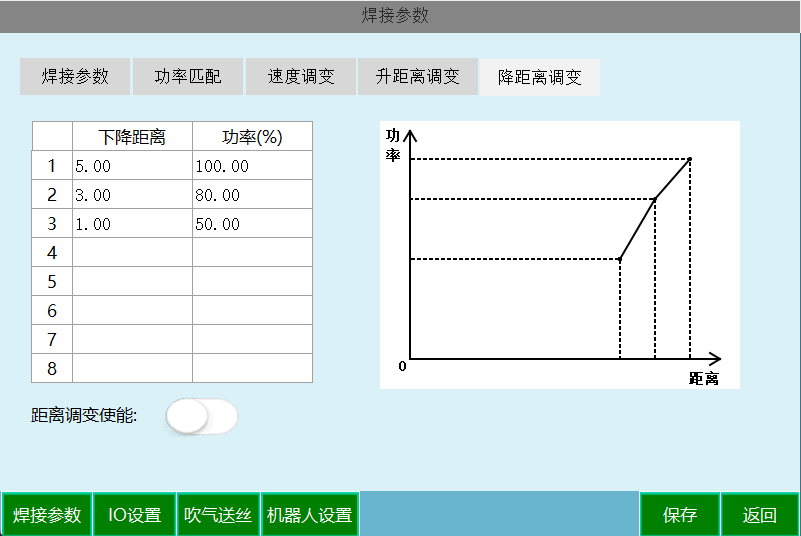
Laser vision tracking and positioning
Laser welding has the advantage of high-precision welding, but the high processing precision also requires high-precision processing position of the welding base material, which poses a significant challenge to the actual production environment.
The iNexBot laser welding system has built-in laser vision tracking and positioning functions. When used in conjunction with laser welding, it can automatically locate the welding seam position, and even if there is a certain error in the processing position, it can be automatically compensated, making the welding process more efficient and the deployment faster.
Dynamic adjustment of mirror lens shape
For a single weldment, there may be multiple different welds that require varying beam sizes and shapes. To avoid the need for manual adjustment of the mirror lens after each weld, the iNexBot laser welding has an integrated function for dynamically adjusting the mirror lens. This feature, combined with dynamic power adjustment, ensures consistent welding by maintaining constant power density on the metal surface despite changes in beam size and shape.
Secondary development system
iNexBot can provide a secondary development package for laser welding processes to meet the personalized needs of users. The package has encapsulated all laser welding functions, allowing users to develop their own laser welding interfaces according to their specific needs and make laser welding processes their own. iNexBot Open Platform
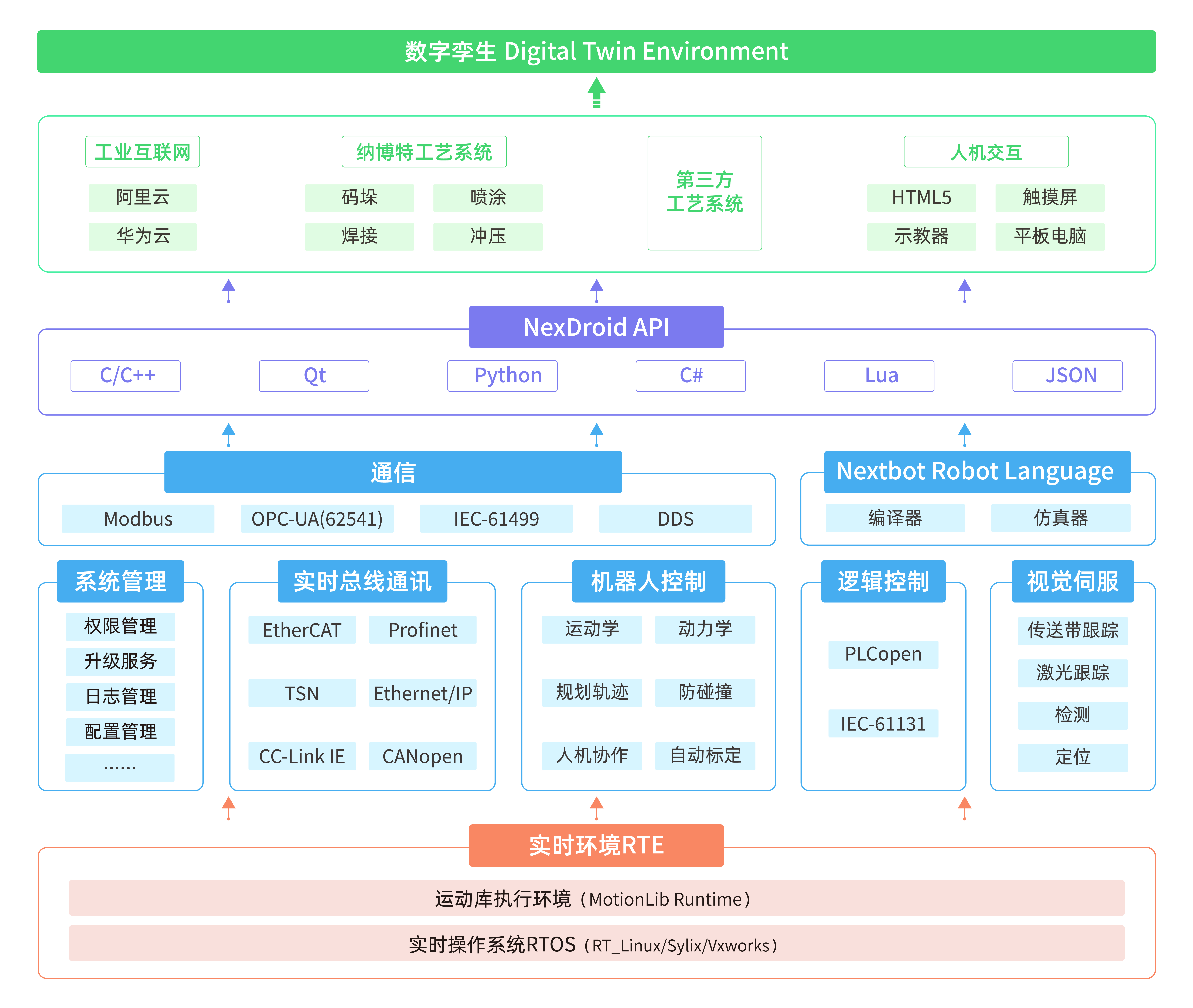