Calibration Series_6-Axis Robot Tool Hand Calibration
2022-05-23
What is Tool Coordinate System?
The center of the flange is the origin of the default tool coordinate system. The direction from the center of the flange to the locating hole is the +X direction, the direction perpendicular to the flange pointing outward is the +Z direction, and finally the Y direction can be determined using the right-hand rule. The new tool coordinate system is derived from the default tool coordinate system.
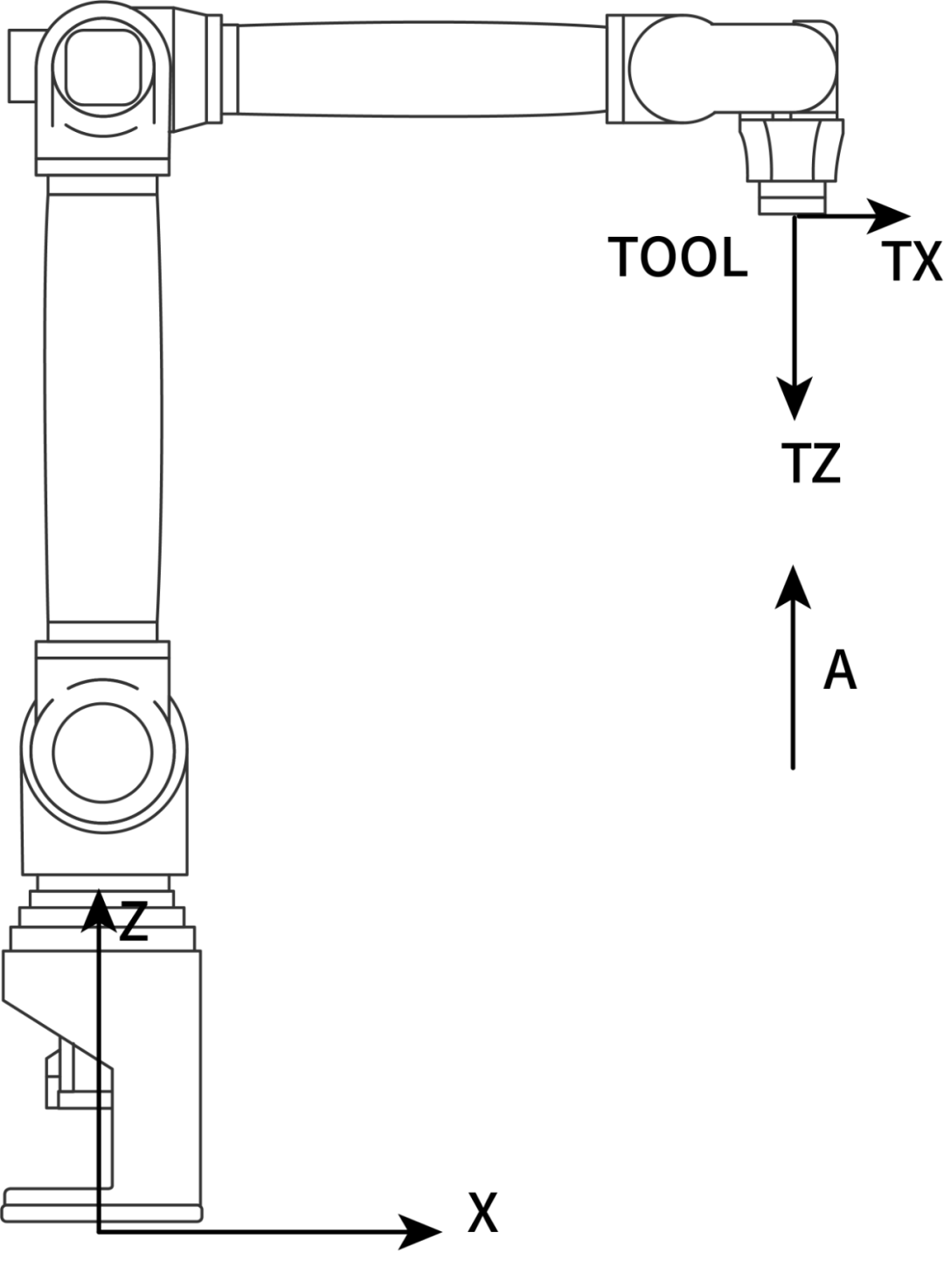
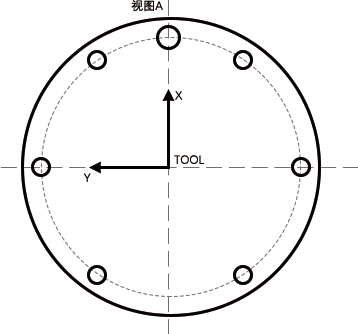
TCP: TOOL CENTER POINT, which refers to the center point of the tool
Robot trajectory and speed: refers to the trajectory and speed of the TCP point.
The TCP is generally set at the center of the gripper, the end of the welding wire, the front end of the spot welding arm, etc.
To describe the position of an object in space, a coordinate system must be fixed on the object, and the pose of the coordinate system (origin position and orientation of the three coordinate axes) must be determined. Therefore, 7 degrees of freedom (DOF) are required to fully describe the pose of the rigid body [1]. For industrial robots, a tool (Tool) is installed on the end flange to perform operations. In order to determine the pose of the tool (Tool), a Tool Coordinate System (TCS) is bound to the Tool, and the origin of the TCS is the Tool Center Point (TCP). When programming the robot's trajectory, the pose of the TCS in other coordinate systems needs to be recorded in the program for execution.
Industrial robots generally have a TCS defined in advance, and the XY plane of the TCS is bound to the flange plane of the sixth axis of the robot, and the origin of the TCS coincides with the center of the flange. Obviously, the TCP is at the center of the flange. ABB robots call TCP tool0, and REIS robots call it _tnull. Although the default TCP can be used directly, in actual use, such as welding, users usually define the TCP point to the tip of the welding wire (actually the pose of the torch tool's coordinate system relative to the tool0 coordinate system), so the position recorded in the program is the position of the tip of the welding wire, and the posture recorded is the posture of the welding torch rotating around the tip of the welding wire.
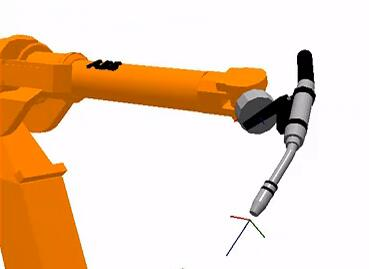
Thinking
The tool coordinate system is a research object in motion, but what role does it play in the actual debugging process? How were the gripper postures and positions in Figures 1 and 2 adjusted?
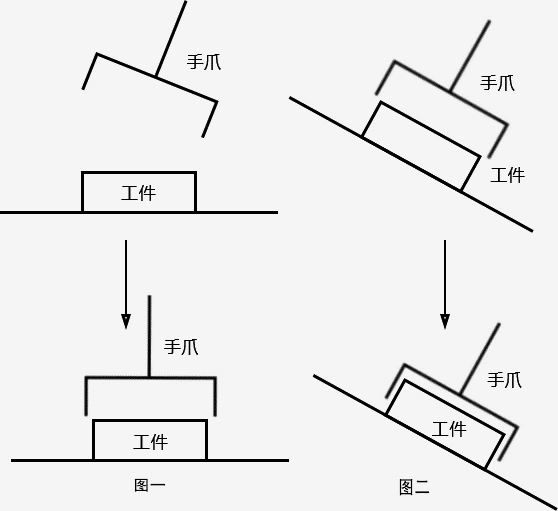
Two conjectures can be made based on thinking:
Conjecture 1: If the gripper in Figure 1 has a rotation point, the gripper can be rotated directly around this rotation point.
Conjecture 2: If there is a forward direction of the gripper in Figure 2, the gripper can be moved directly to that direction.
Conclusion: The role of establishing the tool coordinate system:
Establish the TCP point of the tool (i.e., the center point of the tool) to facilitate the adjustment of the tool state.
Determine the feed direction of the tool to facilitate the adjustment of the tool position.
Characteristics of the Tool Coordinate System
The new tool coordinate system is derived from the default tool coordinate system, and the position and orientation of the new tool coordinate system always maintain an absolute position and posture relationship with the flange, but it changes continuously in space.
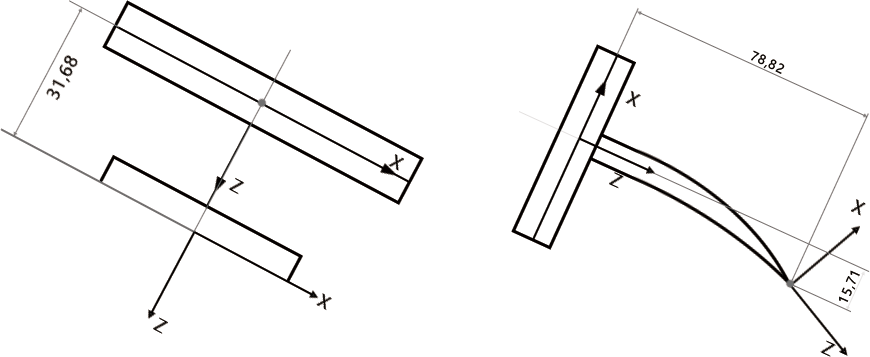
When to use tool hand parameters: When attitude rotation around X, Y, and Z axes is required, it is necessary to calibrate the tool hand
When not to use the tool hand parameters: The robot itself only does Z-axis attitude rotation, and the tool end is located on the centerline of the axis 6 flange; the tool hand parameter can be left off in this case.
What is Tool Hand Calibration?
Tool hand calibration is the process of using the tool hand end to align with a fixed point in space and selecting a certain number of points to calculate the tool size and attitude.
The following conditions must be met to use tool hand calibration:
- Robot type: 6-axis serial multi-joint, 6-axis cobot
- The tool end has a feature that can be aligned with the calibration cone: pointed tool hand
- The robot body parameters are accurate
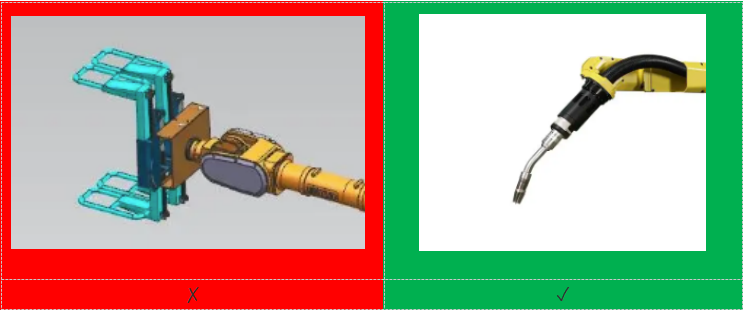
Note: If the tool does not have a tip or cannot be aligned with the calibration cone, a specific pointed object can be clamped with a gripper for calibration. The calibration accuracy depends on how the pointed object is placed.
How to Choose a Calibration Method
The characteristics of the calibration methods are as follows:
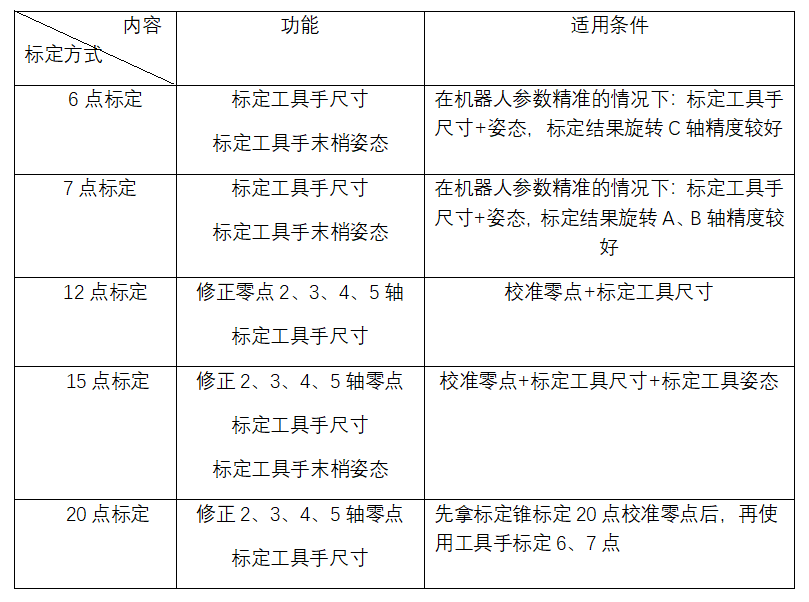
Scenario 1: The robot has undergone laser calibration + using a welding torch
Recommendation: Just use the 6-point calibration method to calibrate the tool hand, and verify the robot calibration results after calibration.
Scenario 2: The robot has not undergone laser calibration + using a welding torch
Recommendation: Just use the 12-point calibration method to calibrate the tool hand, and verify the robot calibration results after calibration.
Scenario 3: Calibrate the palletizing gripper
Recommendation: First try to directly input the tool size, and if the size is unknown, then use the 6-point calibration method
- Prepare a pointed object that can be gripped by the gripper, and place it as centrally as possible in the gripper
- Just use the 6-point calibration method to calibrate the tool hand
- Verify the robot calibration results after calibration
Scenario 4: The zero point of the robot is lost, and the zero point position calibrated according to the alignment hole is deviated
Recommendation:
- Prepare a calibration tool with a small tool size, and the end of the tool should be located as close as possible to the centerline of the axis 6 flange
- Use the 20-point calibration method to calibrate the zero point
- After the 20-point calibration, switch to the actual tool to perform the 6-point calibration
- Verify the calibration results of the robot after calibration
Scenario 5: After the 6-point calibration, there is a significant rotation error in axes A and B, which does not meet the usage requirements
Recommendation: Switch to 7-point calibration