Robot Design
What is an industrial robot?
Generally speaking, an industrial robot consists of three main parts and six subsystems.
The three main parts are the mechanical part, the sensing part, and the control part.
The six subsystems can be divided into mechanical structure system, drive system, perception system, robot-environment interaction system, human-machine interaction system and control system.
Mechanical structure system
From the perspective of mechanical structure, industrial robots can be broadly classified into serial robots and parallel robots. The characteristic of a serial robot is that the movement of one axis will change the coordinate origin of another axis, while the movement of one axis in a parallel robot will not change the coordinate origin of another axis. Early industrial robots mainly adopted serial mechanisms. A parallel mechanism is defined as a closed-loop mechanism consisting of a moving platform and a fixed platform connected by at least two independent kinematic chains, with two or more degrees of freedom, and driven in a parallel manner. A parallel mechanism consists of two main components, namely the manipulator and the wrist. The manipulator's workspace has a significant impact on the operational space, and the wrist is the part that connects the tool and the main body. Compared to serial robots, parallel robots have advantages such as high stiffness, structural stability, large load-bearing capacity, high positional accuracy, and low motion load. In terms of kinematic solutions, the forward kinematics of a serial robot is relatively easy, while the inverse kinematics is difficult; conversely, the forward kinematics of a parallel robot is difficult, while the inverse kinematics is relatively easy.
Drive system
A drive system is a device that provides power to mechanical structure systems. Depending on the power source, drive systems can be classified into four types: hydraulic, pneumatic, electric, and mechanical. Early industrial robots used hydraulic drive systems. However, hydraulic systems have issues such as leaks, noise, and unstable low speeds. In addition, power units are bulky and expensive. Currently, hydraulic drive systems are only used in large heavy-duty robots, parallel processing robots, and some special applications. Pneumatic drive systems have advantages such as high speed, simple system structure, easy maintenance, and low price. However, pneumatic devices operate at low pressure and are not suitable for precise positioning. They are mainly used for driving end effectors of industrial robots. Pneumatic grippers, rotary cylinders, and pneumatic suction cups can be used for grasping and assembly of medium to small load objects. Electric drive systems are the most commonly used drive systems. They are characterized by convenient power supply, fast response, high driving force, easy signal detection, transmission, and processing. They can also employ various flexible control methods. Stepper motors or servo motors are commonly used as driving motors, although direct drive motors are also used, but they are costly and have complex control requirements. The reducers that are typically used in conjunction with the motors include harmonic reducers, cycloid reducers, and planetary gear reducers. Due to the high demand for linear motion in parallel robots, linear motors have been widely used in this field.
Perception system
The robot perception system converts various internal state information and environmental information of the robot from signals into data and information that the robot itself or other robots can understand and apply. In addition to perceiving mechanical quantities related to its own work state, such as displacement, velocity, and force, visual perception technology is an important aspect of industrial robot perception. Visual servo systems use visual information as feedback signals to control and adjust the position and attitude of the robot. Machine vision systems have also been widely used in various aspects such as quality inspection, workpiece recognition, food sorting, and packaging. The perception system consists of internal sensor modules and external sensor modules, and the use of intelligent sensors improves the robot's maneuverability, adaptability, and level of intelligence.
Robot-environment interaction system
Robot-environment interaction system is a system that enables robots to interact and coordinate with devices in the external environment. Robots are integrated with external devices to form a functional unit, such as a processing and manufacturing unit, welding unit, assembly unit, etc. It can also be multiple robots integrated as a functional unit to perform complex tasks.
Human-machine interaction system
Human-machine interaction system is a device that connects humans with robots and allows them to participate in robot control. Examples include standard terminals of computer, command consoles, information display boards, and danger signal alarms.
Control system
The task of a control system is to govern the executive mechanisms of a robot to accomplish specified motions and functions based on the robot's job instructions and the signals fed back from sensors. If the robot does not have feedback characteristics, it is an open-loop control system; if it has feedback characteristics, it is a closed-loop control system. According to the control principles, it can be classified into program control systems, adaptive control systems, and artificial intelligence control systems. According to the form of motion control, it can be classified into point-to-point control and continuous trajectory control.
Types of robots supported by NexDroid
The NexDroid control system can support various types of robots, including but not limited to the following:
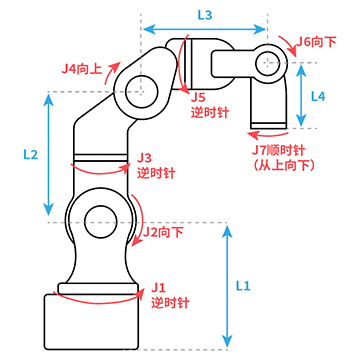
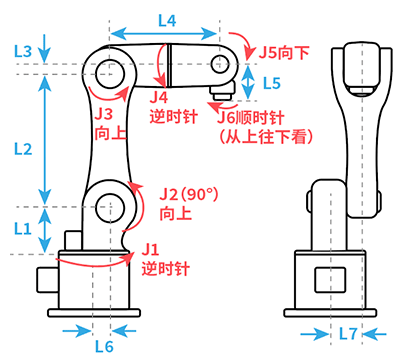
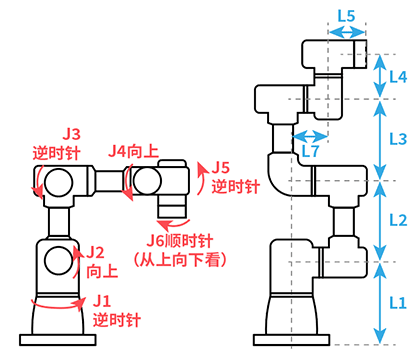
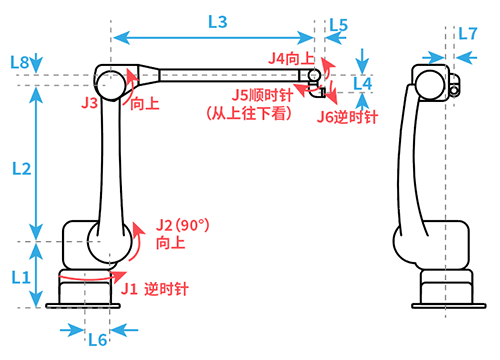
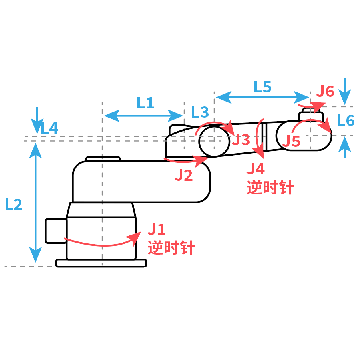
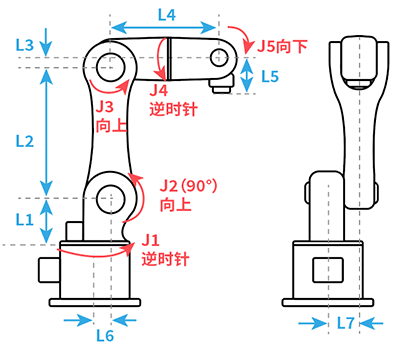
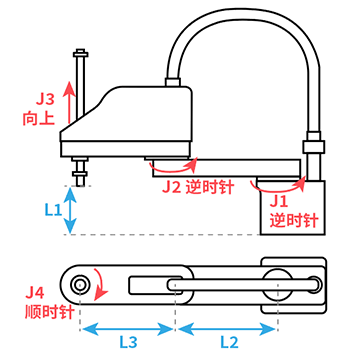
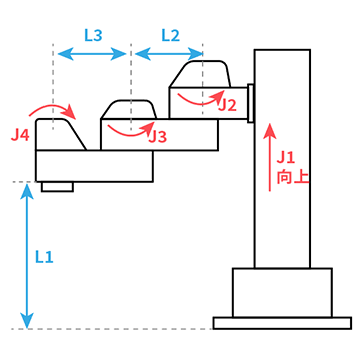

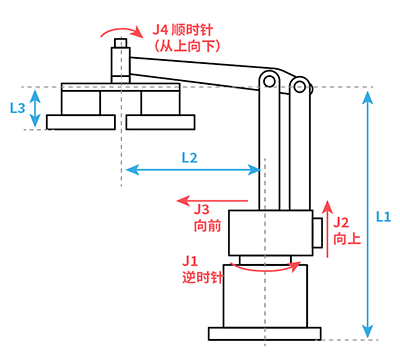
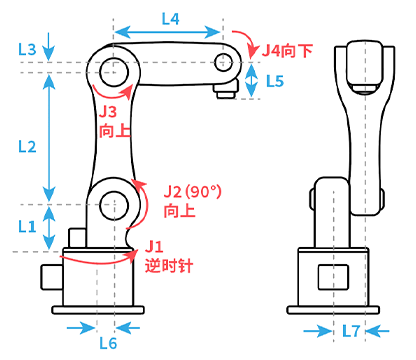
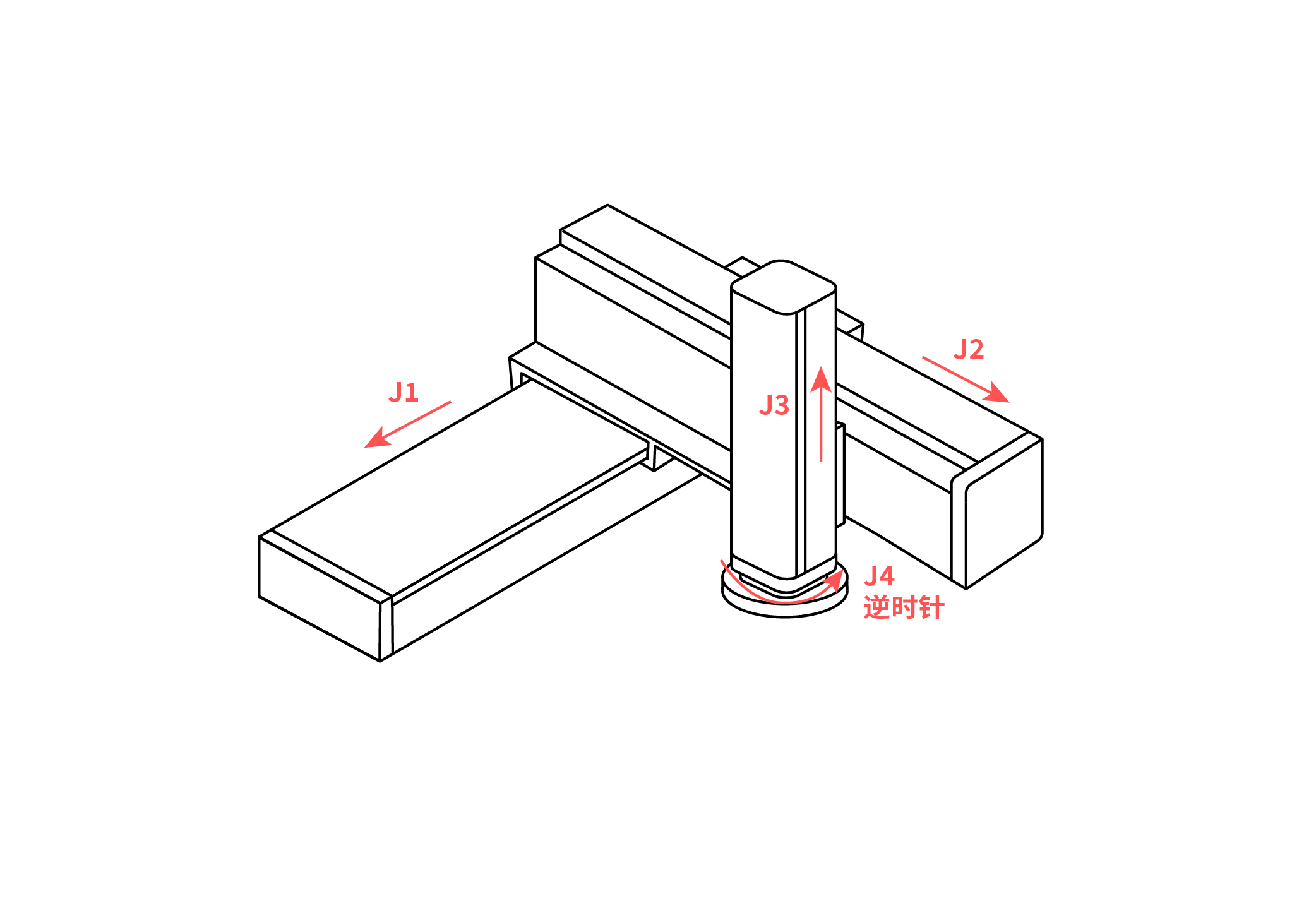
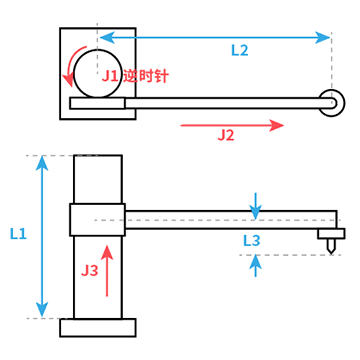
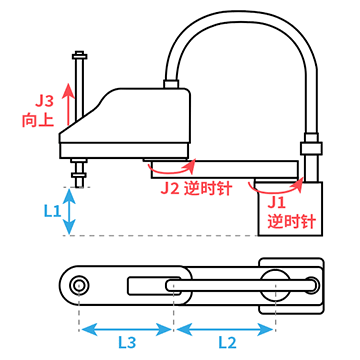
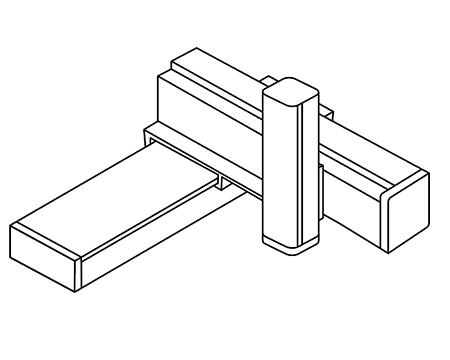
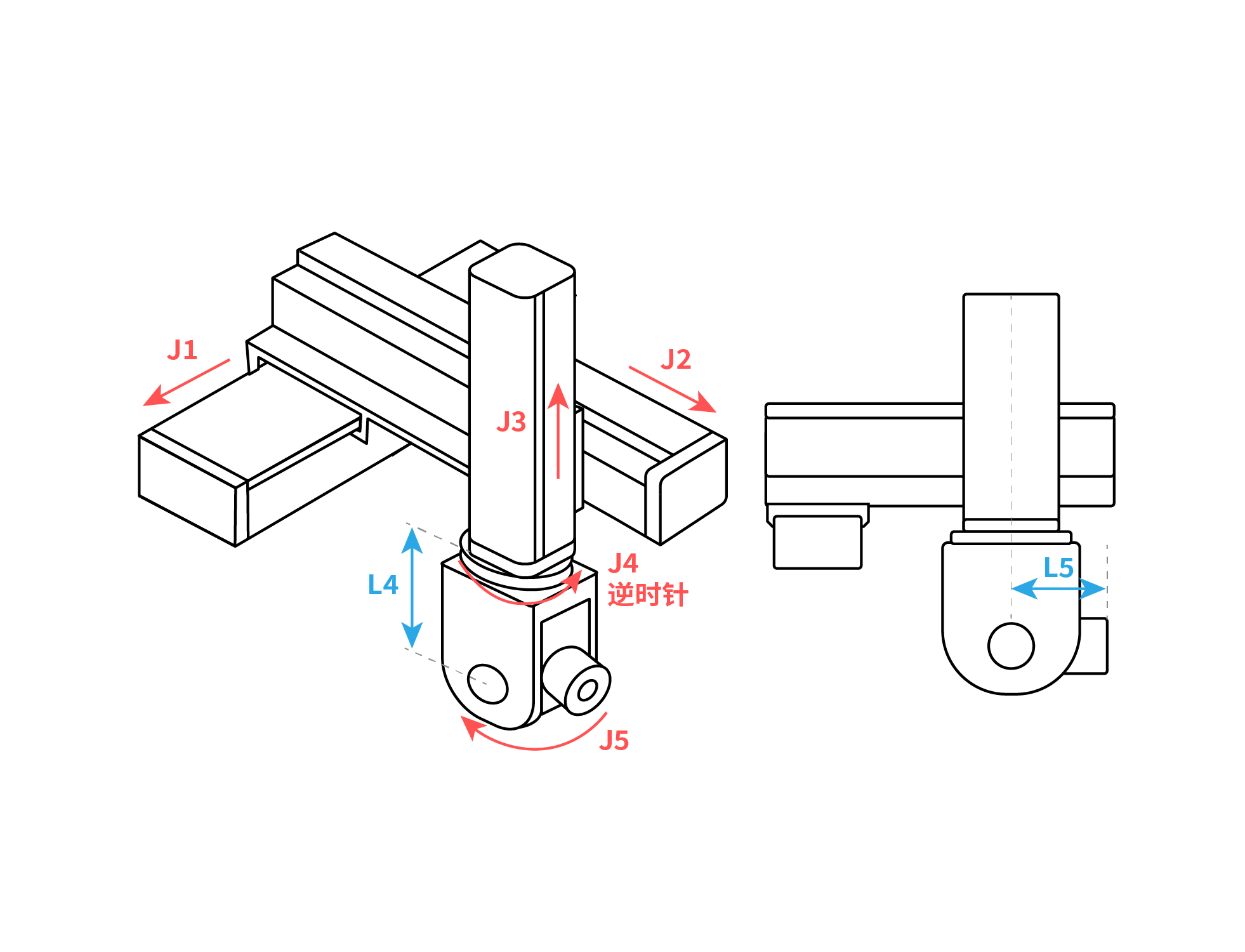
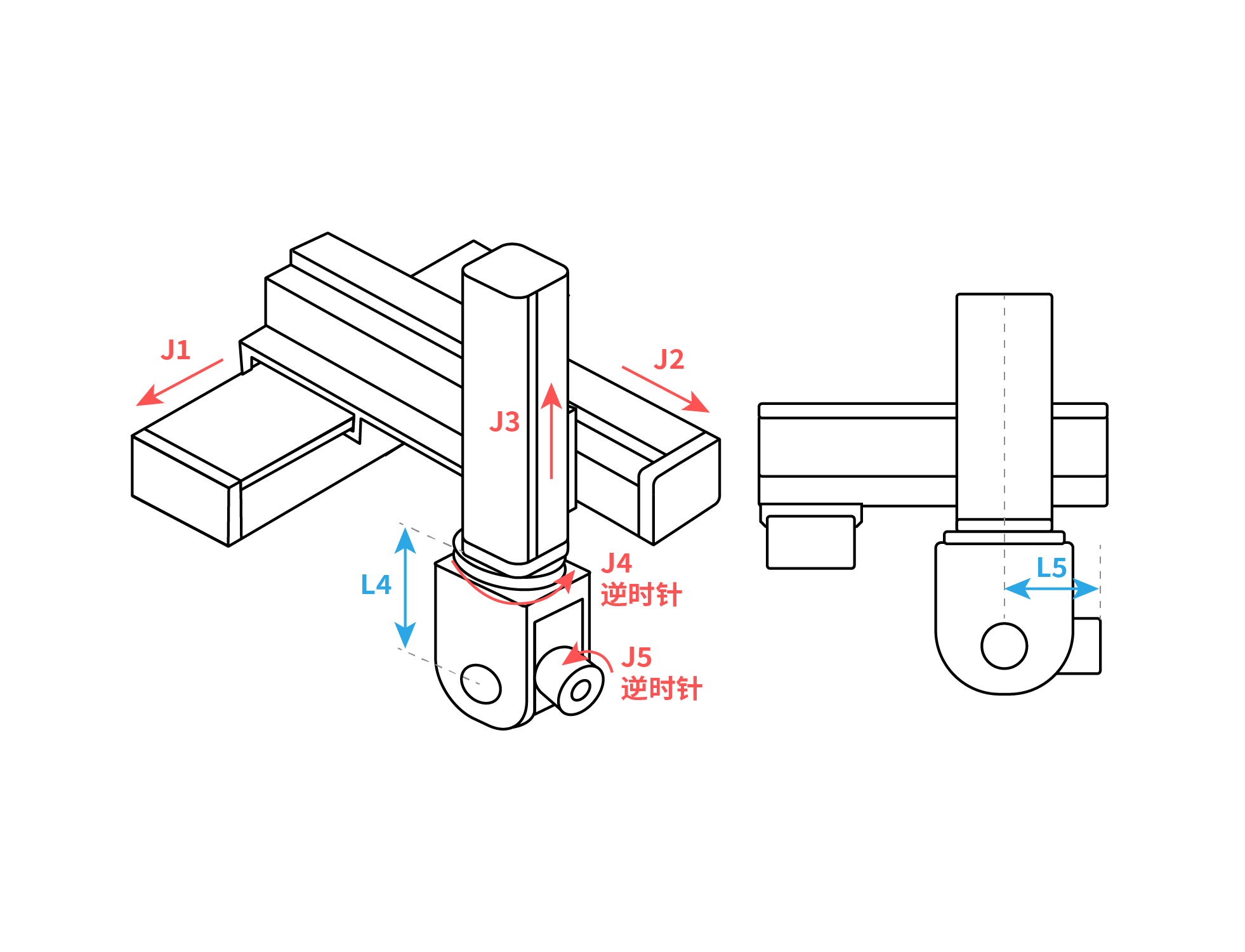
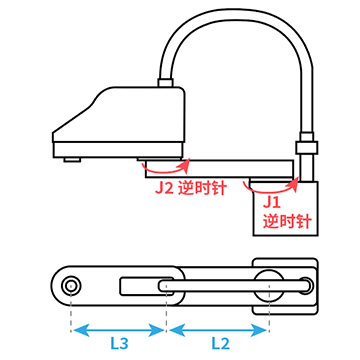
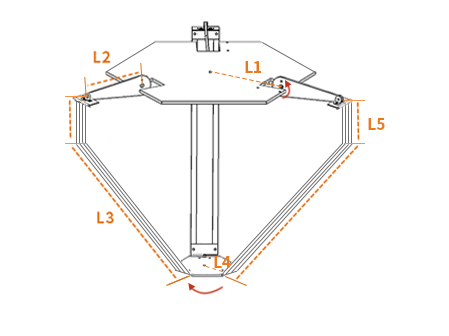
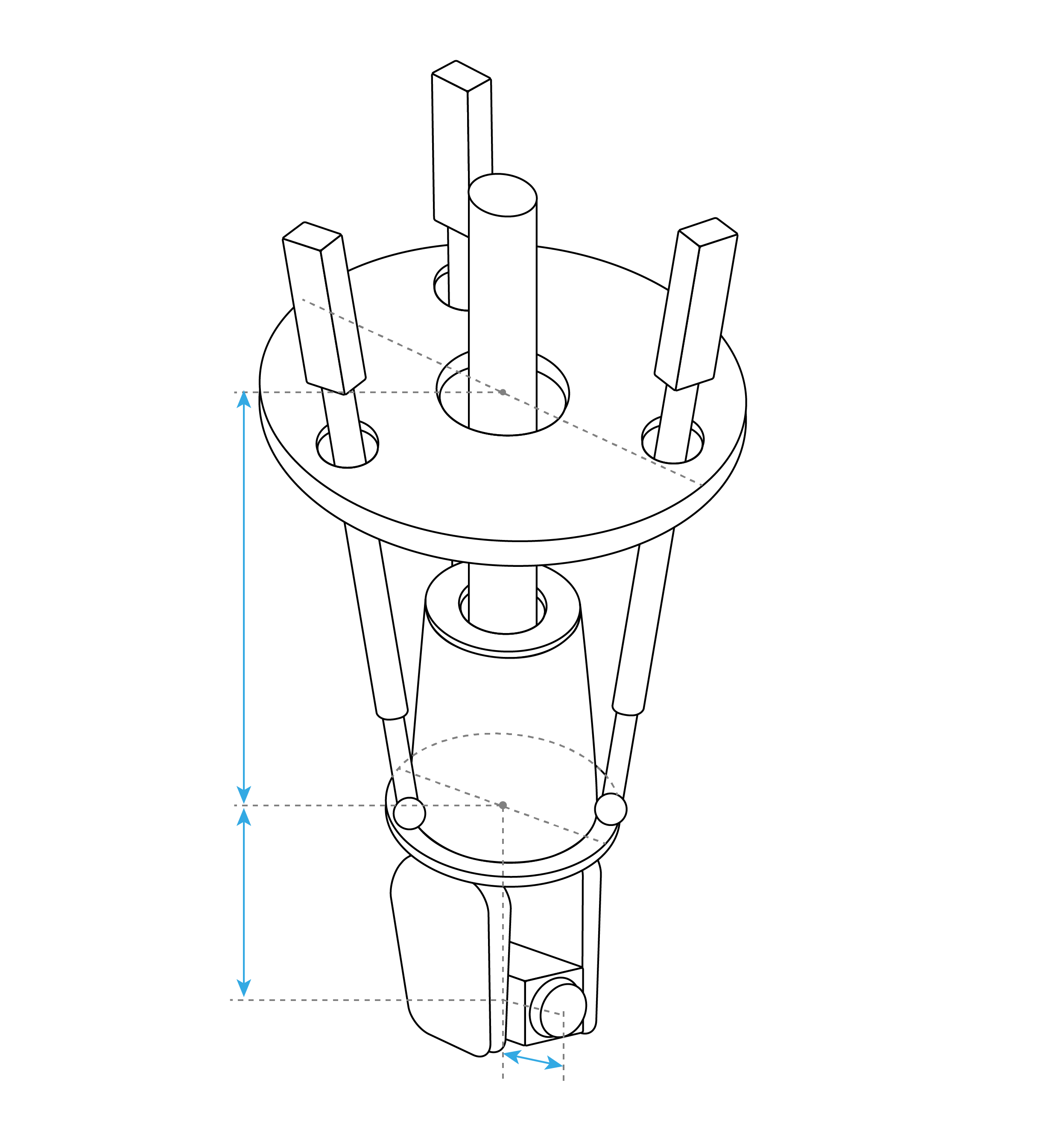
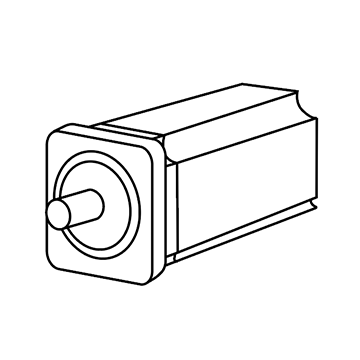
Types of external axes supported by NexDroid
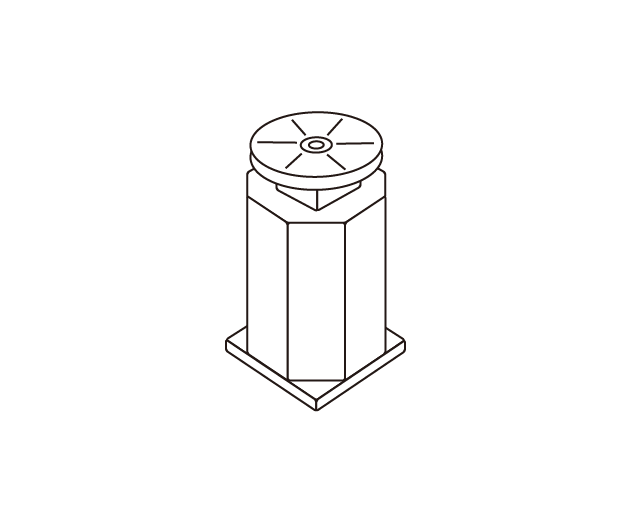
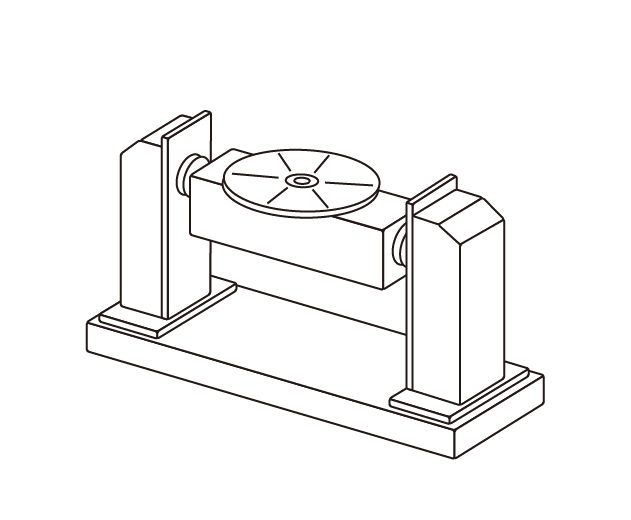
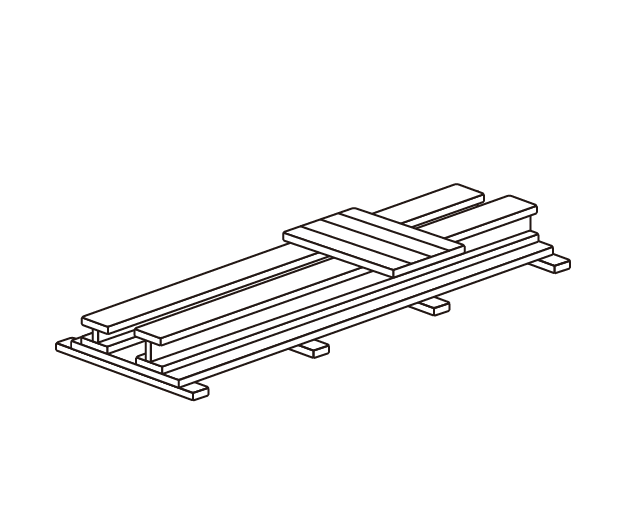
Servo models supported by NexDroid
- Tsino Dynatron R Series
- Tsino Dynatron RC Series
- Tsino Dynatron RD Series
- Tsino Dynatron A8
- Tsino Dynatron RA Series
- Tsino Dynatron CS Series
- JoTong
- JoTong_6
- HANS
- Panasonic MADLN05BE
- Panasonic MADLN15BE
- Panasonic MADLN25BE
- Panasonic MADLN55BE
- Panasonic MEDLN83BE
- Panasonic MCDHT3520BA1
- Panasonic MDDHT3530BA1
- Panasonic MADHT1507BA1
- Panasonic MADHT1505BA1
- STEP AS260_1
- STEP AS260_3
- STEP AS260_4
- THINKVO i3DW
- THINKVO i3DS
- HTSN ASD6_3
- HTSN ASD6_4
- HCFA X3E
- HCFA A2
- ESTUN
- EURA DUAL-AXIS
- Servotronix CDHD
- Servotronix DDHD
- TECO JSDG2
- TECO JSDG2S
- Maxsine EP3
- Maxsine EP3E_6
- ADTECH QXE
- DELTA ASDA_A2
- RUKING
- YAKO
- INVT DA200
- EMP
- XINJE DS5
- ASAGE
- Kaiserdrive
- SANYO
- DAINMU
- MT
- 3PHIS
- ZZ Motion WA
- Techservo
- Donlim
- INOVANCE_4
- INOVANCE_IS620
- ZeroErr
- VMMORE
- SHINKAWA
- DEALOUR
- SINEE
- HUACHENG
- SERVODE_625
- More (can be added by yourself)...