Metal Welding
Metal welding is mainly divided into gas shielded welding, argon arc welding, and laser welding.
Laser Welding
Laser Welding Industry Solution
Argon Arc Welding
Argon arc welding is suitable for welding carbon steel, alloy steel, stainless steel, refractory metals such as aluminum and aluminum-magnesium alloys, copper and copper alloys, titanium and titanium alloys, as well as ultra-thin plates with a thickness of 0.1mm. It can perform all-round welding, especially in the inaccessible parts of complex weldments.
Advantages:
- It can weld most metals and alloys except for aluminum and tin, which have a very low melting point.
- AC argon arc welding can be used for welding aluminum and aluminum-magnesium alloys, which have relatively active chemical properties and are prone to the formation of oxide films.
- No welding slag and spatter during welding.
- It can perform all-round welding. You can choose pulsed argon arc welding to reduce heat input. It is suitable for welding 0.1mm stainless steel with high arc temperature. It has the advantages of low heat input, fast speed, small heated area, and small welding deformation.
- The filler metal and the amount added are not affected by the welding current.
Gas Shielded Welding
Gas shielded welding usually refers to the welding method using carbon dioxide or argon shielding gas. It uses welding wire instead of welding rod. CO2 gas shielded welding has high efficiency, while argon gas shielded welding is mainly used for materials such as aluminum, titanium, stainless steel, etc.

Advantages
The iNexBot control system enables the robot to move smoothly and uniformly during the welding process, allowing the welding job to be completed faster and with more beautiful seams.
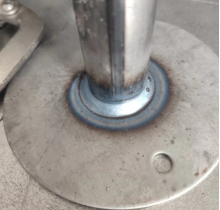
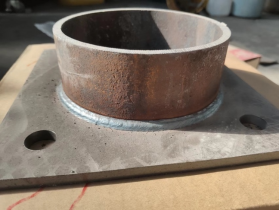
Various types of seams can be welded with the multiple interpolation methods built into the iNexBot control system.
The iNexBot control system has multiple welding instructions that can fully customize the entire welding process.
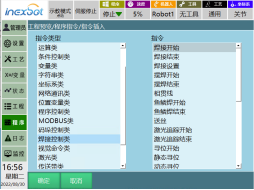
Users can customize welding parameters with flexible configuration options and an intuitive, streamlined interface.
This system can be used for welding various types of materials with just a few simple configurations.
The iNexBot control system has market-validated welding processes, eliminating the need for additional process packages, users can simply configure the system and start using it.
- Faster, more stable and smarter
- Full-featured, supporting multiple types of seams
- Diverse instructions, supporting various customized processes
- Easy to use, flexible parameter configuration methods
- Suitable for sheet metal, aluminum, alloy and other materials
Reignition
If there is rust, oil and other debris at the arc ignition position of the workpiece, it may lead to ignition failure. This situation can be effectively prevented by repeating the arc ignition operations using the reignition function.
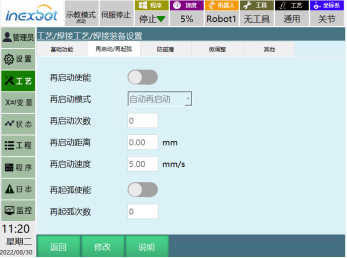
Restart
If a robot stops due to reasons such as arc-quenching, starting it again directly will result in incomplete welding. By using the arc quenching restart function, the robot can move back a specified distance at a specified speed after the arc is quenched, and then continue its operation under normal welding conditions.
Scrape
When the "Scrape" is activated, the robot will move back and forth even if the arc ignition fails. If the arc ignition is successful during this movement, it will move back a certain distance and then continue with normal welding.
Gas pre-flow, arc-quenching
Execute the arc ignition instruction and begin wire feeding at a slow speed before the robot reaches the arc ignition position. When the robot reaches the arc ignition position, the wire contacts the workpiece to ignite the arc. This improves welding efficiency.
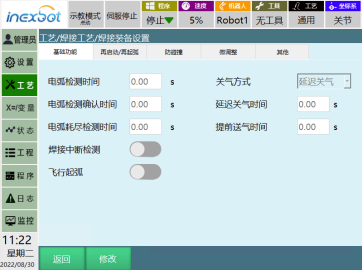
Anti-sticking treatment
Output the anti-sticking current and voltage before the end of welding to prevent the wire from sticking.
Automatic wire-stick release
When the arc is quenched, wire sticking sometimes occurs. In order to prevent this from happening, an instantaneous relatively high voltage is output at the end of welding to prevent the wire from sticking.
Laser Tracking
By utilizing laser sensors to obtain the accurate position of the weld seam, the robot can adjust its end effector position during the welding process, ensuring that the torch always moves along the seam. This ensures perfect formation of welds, reduces thermal load, increases productivity, keeps the torch in an ideal position, compensates for production, equipment and operational tolerances, and reduces programming work and achieves consistent, reproducible connections for complex weldments.
Multi-Layer Multi-Pass Welding
Multi-layer multi-pass welding is suitable for welding thick plates with wide and deep joints. It can reduce heat input, minimize deformation, and lower the probability of defects. It is applicable to various types of welds, such as butt, fillet, or plug welds.
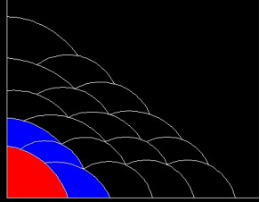
Weaving Welding (Sine/Triangular/Circular)
During the welding process, the robot weaves regularly to control the weld width and improve the quality of interlayer and surface welding.
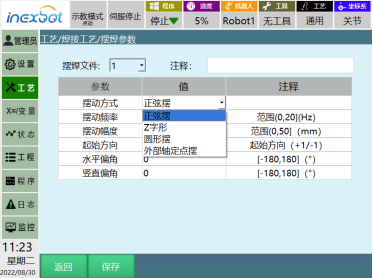
Intersecting Line
Our system supports intersecting line welding with or without positioners. Only the radius and position of the two cylinders that generate the intersecting lines need to be calibrated. For intersecting line welding with positioners, the positioner and robot work together to complete the intersecting line trajectory during the welding process. For intersecting line welding without positioners, the robot completes the trajectory alone.
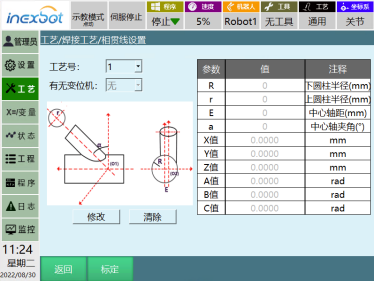
Arc Pressure Tracking Welding
The arc voltage tracking system refers to using the arc voltage as the sensing signal to monitor the voltage during welding in real time. Through the automatic control of the arc height, it is not necessary to adjust the up and down height of the torch when the pipeline is automatically welded, which is automatically completed by the arc voltage tracking system.
After realizing this function, there is no need to worry about the phenomenon of arc breaking during welding due to the unevenness of the weld seam caused by the ovality of the pipe. The arc voltage tracking system will automatically adjust the height of the torch through the automatic control of the arc height.
Arc Tracking Welding
When welding thicker workpieces using arc tracking technology, the fluctuation of current and voltage can be measured and compensated by weaving welding, so as to ensure the quality of the weld seam and save laser cost.
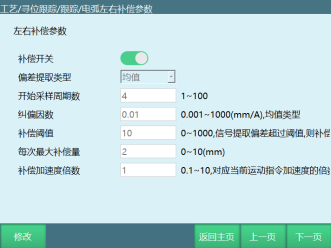
Intelligent Non-Teaching Programming Welding
iNexBot supports drag welding. After identification, the operator can manually drag the robot to the desired position and press the corresponding IO signal to record the position, and finally start welding according to the recorded trajectory.
Compared to traditional manual teaching welding, drag welding has higher flexibility and does not require inserting instructions one by one. It only needs to trigger the IO signal. The welding speed and nonwelding speed can be customized. This function can only be used after completing the dynamics identification.
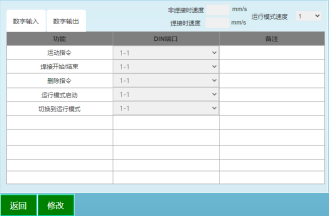