iNexBot NRC series controllers are now integrated with Profinet
iNexBot NRC series controllers are now integrated with Profinet
PROFINET is an open industrial Ethernet standard introduced by PI. It utilizes IT standards such as TCP/IP and is standardized by IEC 61158 and IEC 61784. It offers real-time capabilities and seamless integration with existing fieldbus systems such as PROFIBUS, ASi, Interbus, etc. A PROFINET IO controller can connect up to 512 I/O devices, with no limitations on the entire Ethernet network nodes.
With its openness, flexibility, and superior performance, PROFINET allows the transmission of non-real-time data, such as TCP/IP, on the same bus, enabling the simultaneous deployment of other services. As a result, PROFINET can be applied in areas such as process/factory automation and motion control. It seamlessly integrates with existing fieldbus systems like PROFIBUS, ASi, Interbus, etc. Through PROFINET, deterministic response, microsecond-level hard real-time capabilities, and integrated diagnostic functions can be achieved, making it an ideal foundation for Industry 4.0 communication.
The iNexBot NRC series controllers are now deeply integrated with the Profinet communication protocol, eliminating the need for additional protocol conversion modules. They can be used simultaneously as both master and slave stations.
Before integrating Profinet
To connect a controller to a PROFINET PLC device, you need to use a Modbus-Profinet conversion module or an EtherCAT-Profinet conversion module. Additionally, the controller can only be used as a slave device.
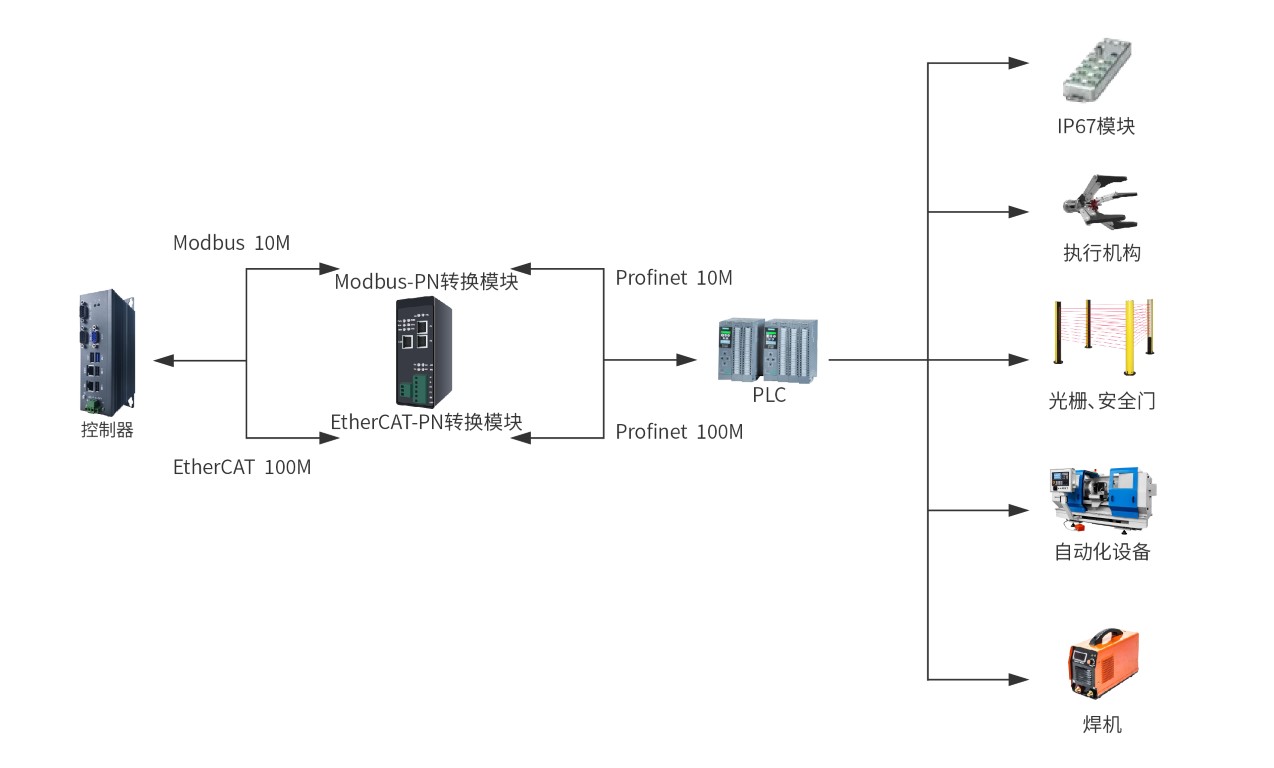
Modbus-Profinet
Due to Modbus's maximum bandwidth being 10M, which falls far short of the 100M standard of Profinet, the transmission speed is low. Even when connected to a Profinet PLC, it can only operate at a slow speed, leading to extremely low operational efficiency.
Modbus can only exchange data using address codes and is unable to handle complex data formats such as XML.
EtherCAT-Profinet
Even if using an EtherCAT-Profinet gateway can achieve the 100M bandwidth of Profinet, the controller can only be used as a slave. It cannot adapt to IO and other slave devices.
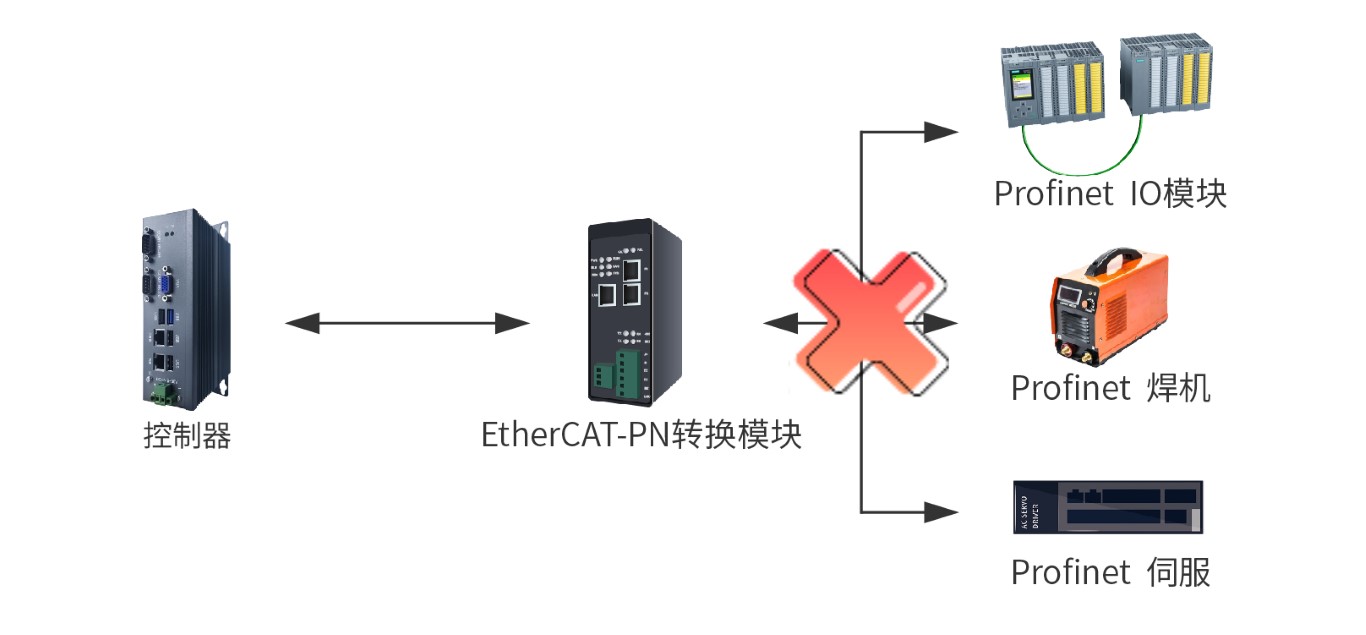
After integrating Profinet
The NRC series controllers provide dedicated Profinet interfaces and can simultaneously act as a master or slave device on the Profinet network. There is no need for additional conversion modules, saving on purchasing and wiring costs. As a master device, NRC controllers can adapt to the majority of Profinet slave devices available on the market, including but not limited to IO modules, welders, spot welding tongs, servos, etc. For devices that have not been previously adapted, only a GSD file is required to quickly complete the adaptation process. As a standard slave device, NRC controllers have already been adapted for all Siemens models of Profinet PLC devices and provide standard GSD files for the master device's adaptation process.
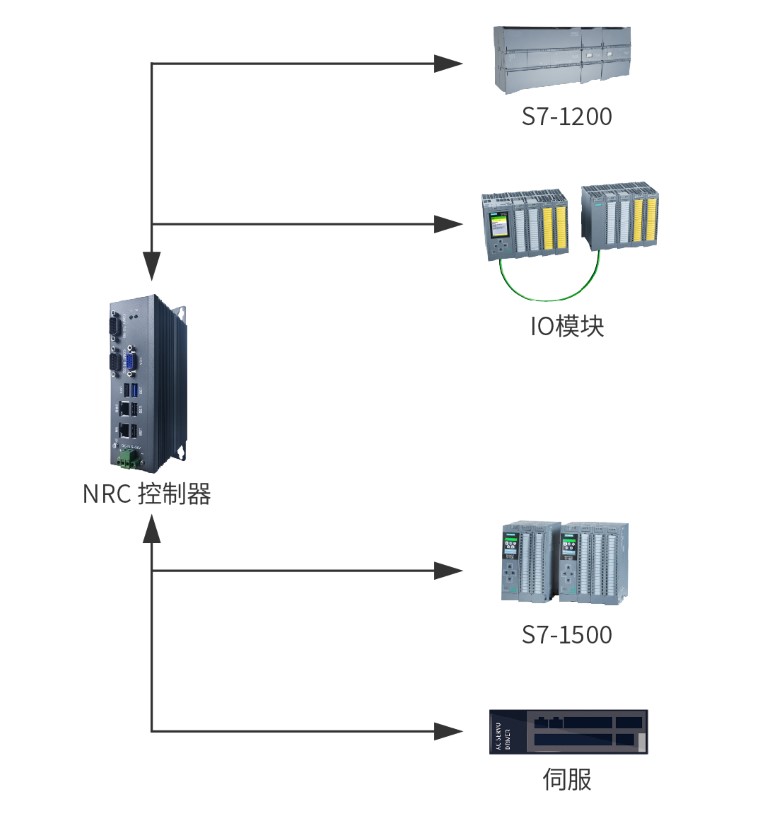
The NRC series controllers can use Profinet's RT/IRT communication mode. For Siemens S7-1200 PLC and IO modules, RT communication can be used, while S7-1500 PLC or devices with high real-time requirements such as servos can use IRT communication. At the same time, the NRC series controllers can also serve as an EtherCAT master to control EtherCAT bus devices, without the need for a binary choice, making it compatible with the majority of field application environments.
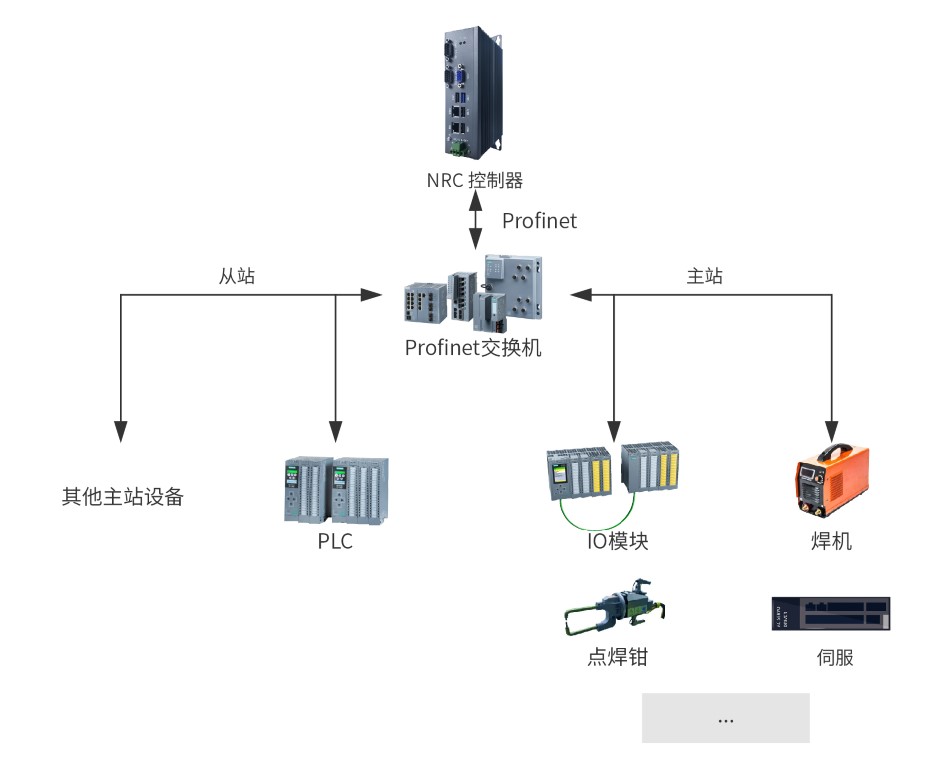