Motion Control Changes the World | iNexBot Control System Launch Event Successfully Held
2024-01-22
Since its establishment in 2015, iNexBot has always adhered to the principles of "innovation, trust, and openness". We are committed to providing efficient and stable control system solutions to customers worldwide. After eight years of deep cultivation, we have witnessed iNexBot's expansion from its foundation in Nanjing to the establishment of research and development centers in Suzhou and Dongguan. Cumulatively, we have sold 20,000+ units and successfully penetrated the international market. Over the past eight years, iNexBot has not only achieved fruitful results in product development but also established a good reputation in the industry.
iNexBot Control System Launch Event Successfully Held
On January 19, 2024, iNexBot Technology held a control system launch event in Suzhou, China. During the event, we reviewed iNexBot's eight-year development journey and outlined the development plans for 2024.
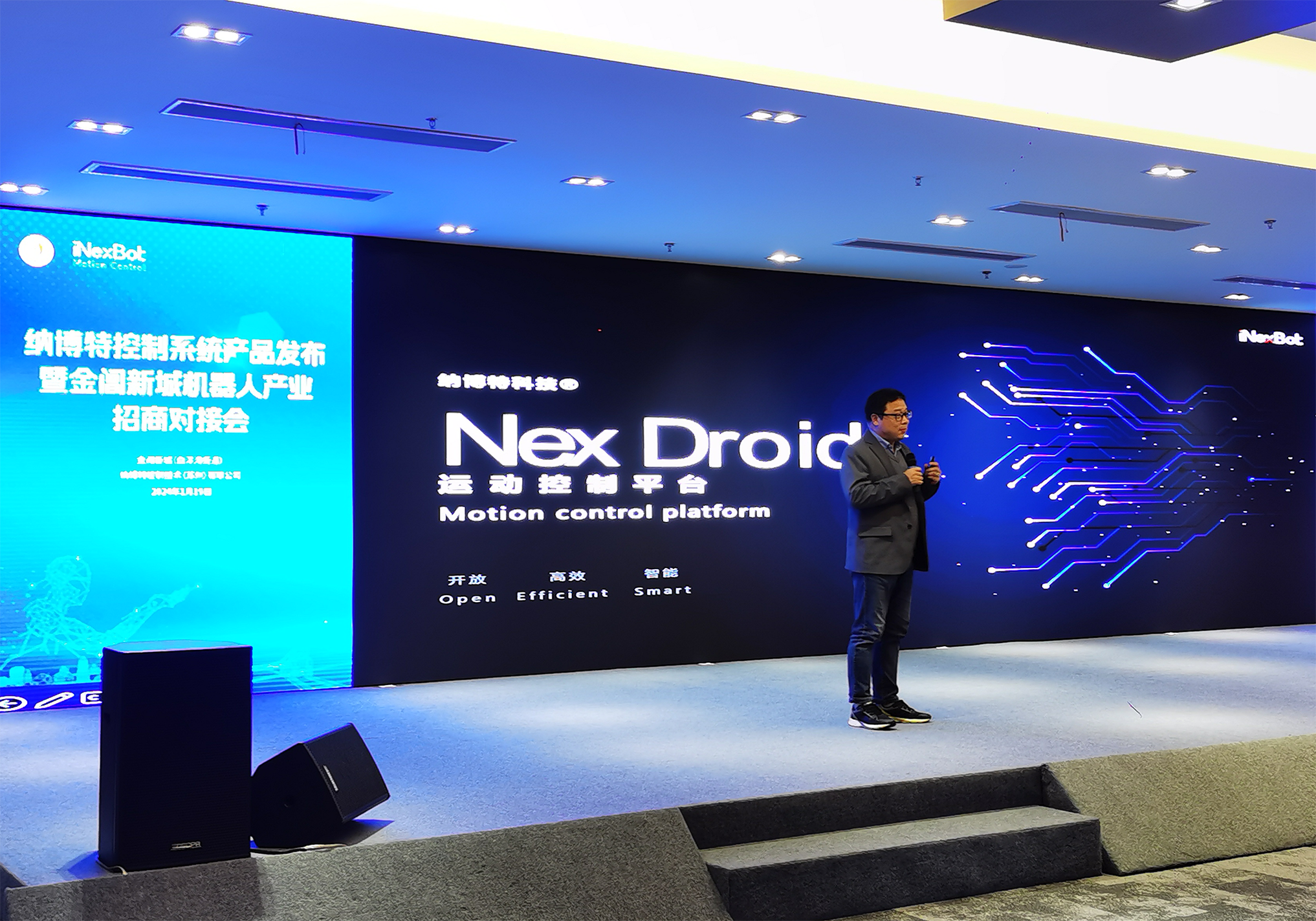


Algorithm:
- We have developed the most comprehensive robot algorithm library in the industry, covering dozens of robot configurations;
- We have standardized the interfaces for kinematics, dynamics, and interpolation methods, allowing users to implement them independently, effectively safeguarding business confidentiality;
- Dynamics is applicable to any model, supports load identification, has high sensitivity to drag and collision, and can achieve soft floating.
Secondary development platform:
- Supports multiple scripting languages such as Python and Lua, making it easy for users to learn and use;
- Provides a language pack module for integrators to translate into any language of their choice, facilitating expansion into overseas markets;
- Provides a Chinese programming language;
- Provides data access interfaces.
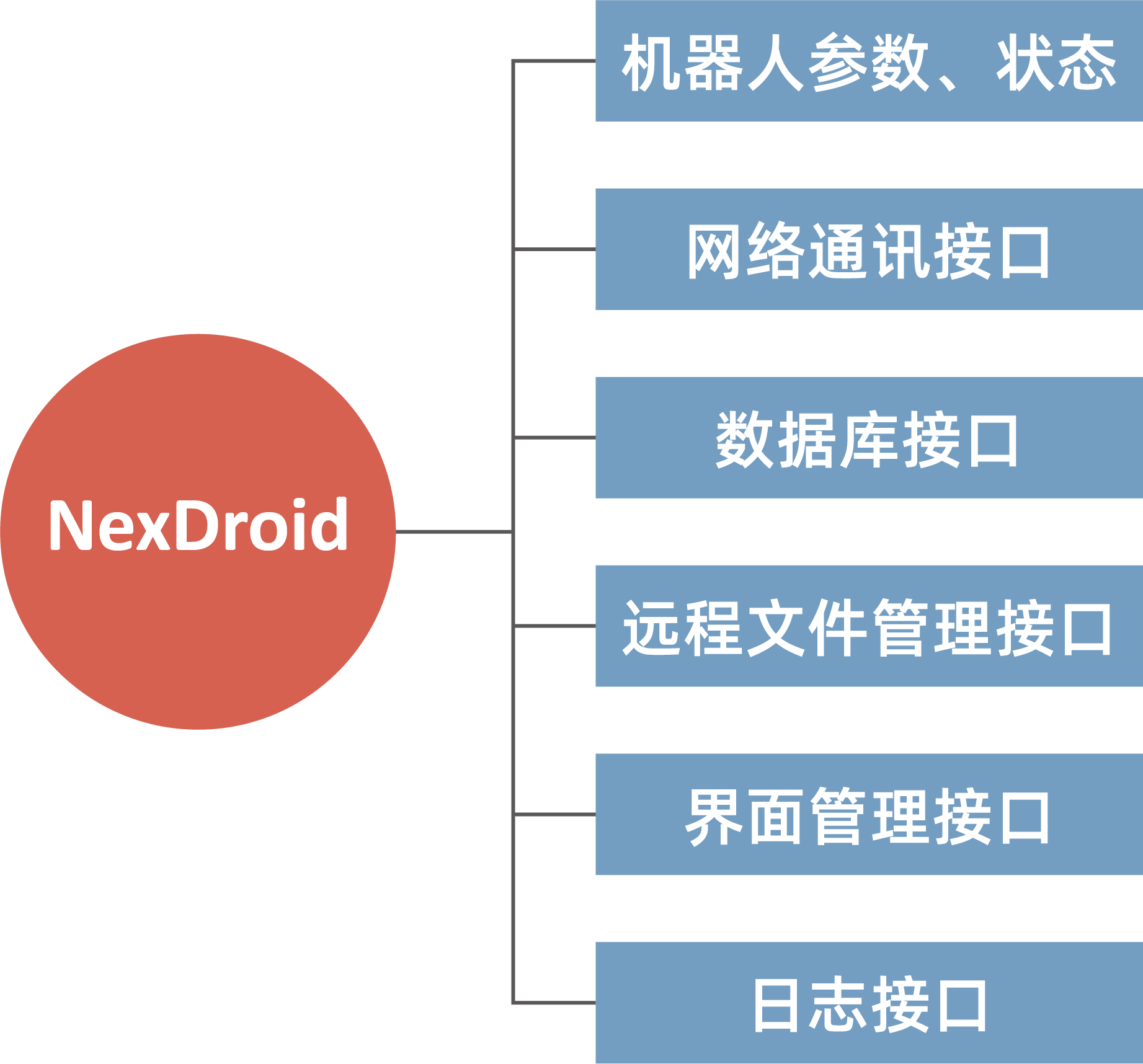
- Supports multiple client connections to the controller, allowing for multi-platform operations and monitoring, facilitating remote cloud-based monitoring of device status.

Process platform:
We have established the most comprehensive process library in industries such as arc welding, spot welding, palletizing, stamping, painting, loading and unloading, engraving, and more.
Communication protocols:
The iNexBot control system is compatible with a variety of communication protocols, including:
- OPC-UA for integrating IT and OT systems
- EtherCAT (ETG member)
- CAN/CANopen/CANApe
- Profinet/Profibus (PN member)
- CCLink IE TSN (CCLink member)
- FINS (Omron)
- EtherNet/IP
- LIN
- AutoSAR (Connected Car)
iNexBot's Product Strategy: Focus, Moderation
Venture into the general motion control market
In addition to the robot market, the general motion control market holds tremendous potential. We were born for robots, but we won't stop there. The general motion control field is our vast ocean.
Establish an open-source community
We will build iNexBot open-source libraries in open-source communities such as Github and Gitee, and actively embrace open-source.
Organize regular nationwide training events
We will conduct training activities nationwide to help users understand and fall in love with the iNexBot control system.
Improve quality and conquer users with excellent quality
We will enhance software quality and ensure zero critical bugs in product delivery. At the same time, we will conduct hardware tests such as CE for all hardware products to ensure their hardware stability. Starting from 2024, we will initiate functional safety certification IEC 61508.
Build a strong research and development team for motion control
We will expand the team from 120 to 200 members, with technical personnel accounting for no less than 80%.
Optimize motion control algorithms
We will continue to optimize motion control algorithms benchmarking against top international control systems like Beckhoff and KEBA.
Vision and control integrated technology
The integration of 2D/3D/laser technology with robots enables them to have perception capabilities.
Drive and control integrated technology
Drive and control integration is the inevitable path towards high performance, and the threshold for drive technology will be significantly lowered.
Mobile and collaborative robots
iNexBot will independently develop navigation, scheduling, and motion control algorithms for collaborative robots.
IDE platform construction
iNexBot's NexDroid Studio IDE platform will provide device management, programming, and simulation functionalities, and integrate Copilot's AI program generation capabilities.
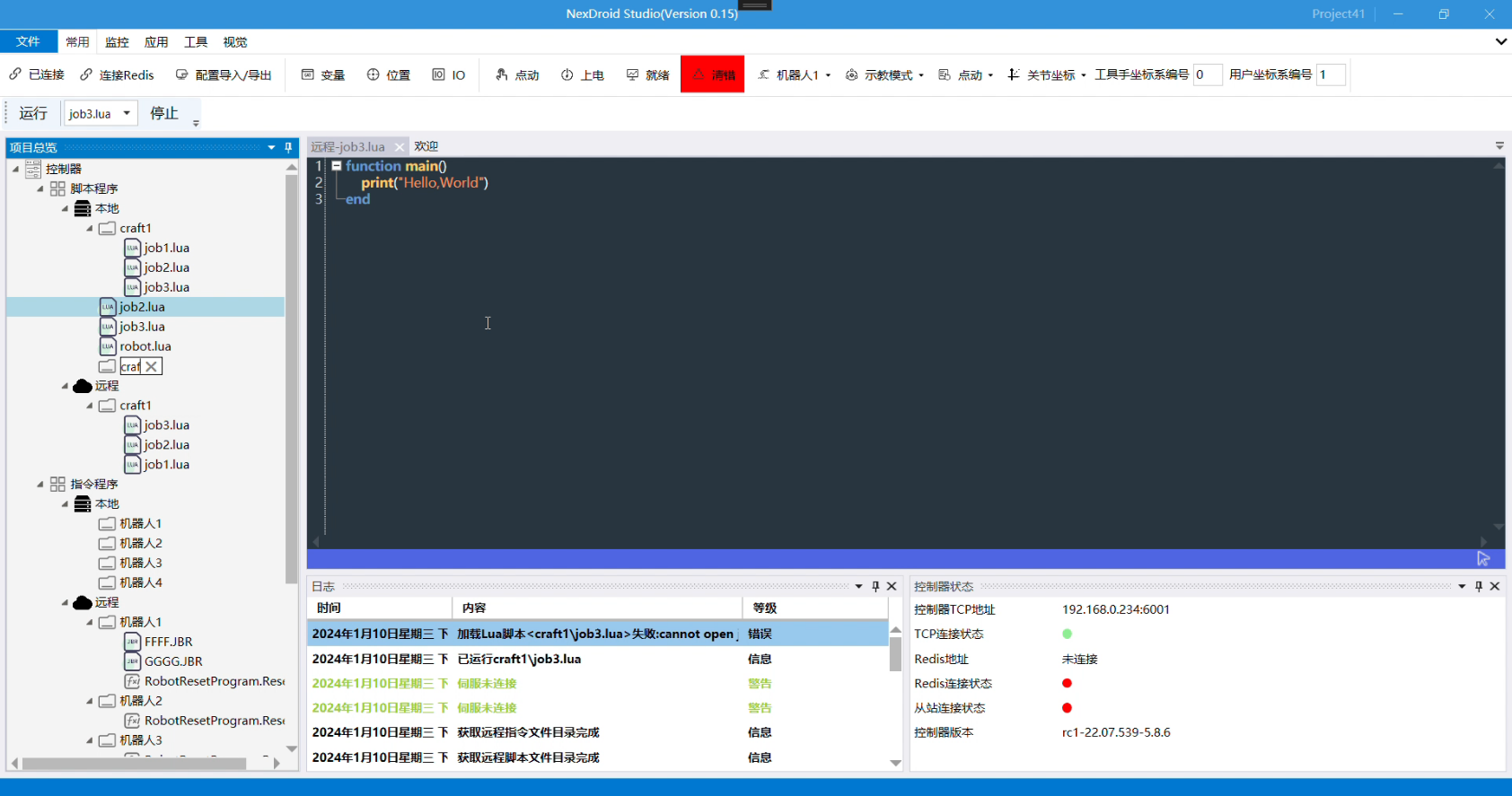
NexDroid Studio includes robot management tools, programming environment, debugging tools, secondary development platform, and industrial Internet platform. It provides local and remote job program file management, and integrates Lua, JBR, and other language servers to offer efficient functions such as syntax and lexical parsing, code completion, and highlighting. Additionally, it integrates Copilot's AI-based code generation services. To facilitate the use of debugging personnel, NexDroid Studio integrates oscilloscopes, command lines, remote file management, ENI editing, virtual simulation, and other debugging tools.
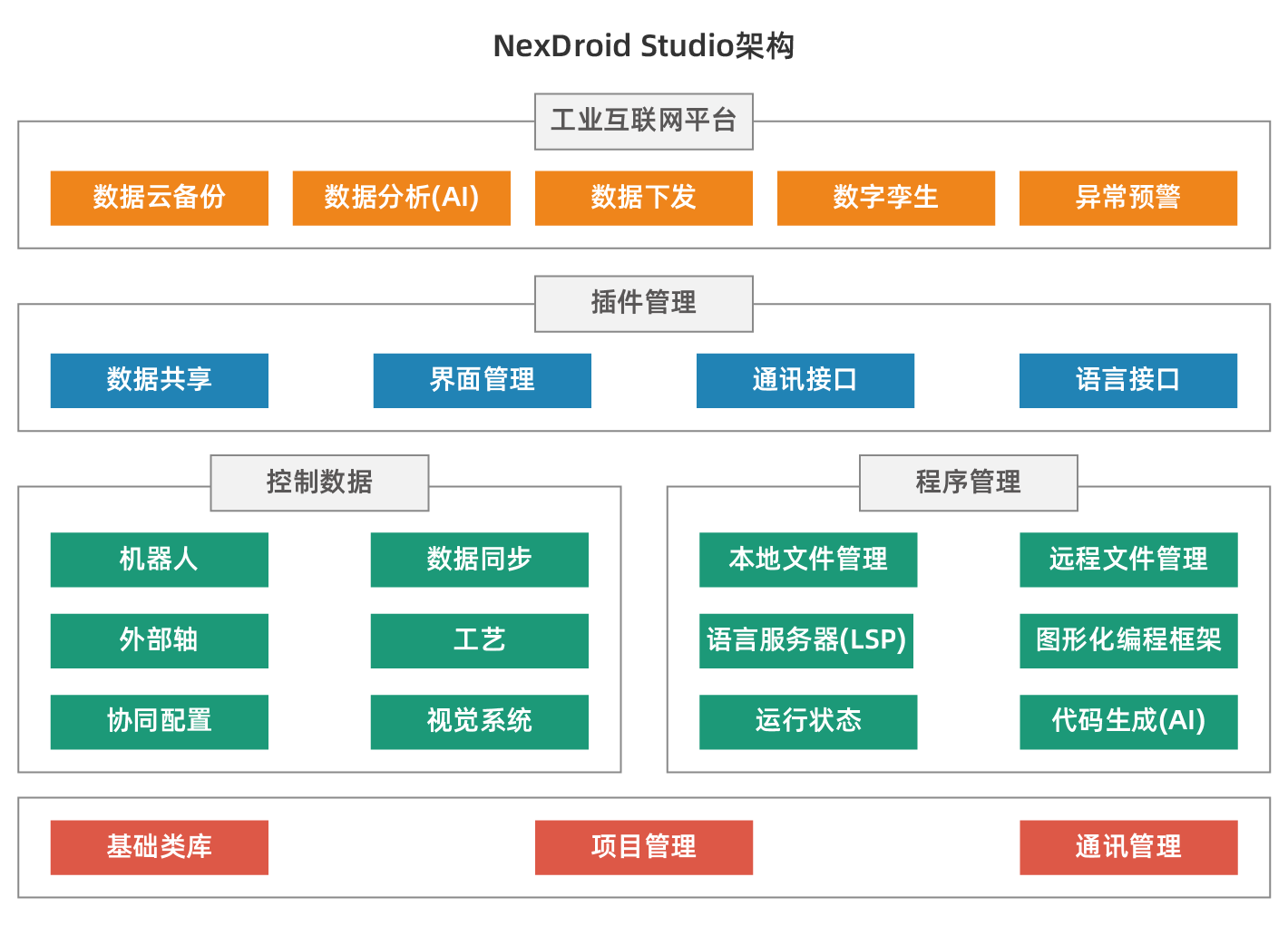
Industrial Internet platform
iNexBot's industrial Internet platform provides capabilities such as industrial data management, AI training, predictive maintenance, and production process improvement. NexDroid Studio industrial Internet platform can back up local control data and running programs to the cloud and deploy them to networked controllers. The digital twin system can faithfully reproduce the operating status of physical devices. With the help of powerful cloud servers, developers can add operators to analyze cloud-based data and use the analysis results to raise alerts for abnormal conditions.
NexDroid 2.0
The target area of NexDroid 2.0 is the robot and general motion control market. The product includes brand-new hardwares, algorithms, IDE platforms, vision and control integrated technology and AI capabilities.
Algorithm optimization
Optimized interpolation, smooth transition, and small line segment algorithms.
- Added smooth transition types: time-based transitions and distance-based transitions.
- Adopted new smoothing algorithms to ensure G3 continuity of curves.
- Based on smooth transitions, a constraint model is established that includes trajectory error constraints, velocity constraints, acceleration constraints, and jerk constraints. Within the constraint model, small line segment trajectory lookahead is conducted to improve operational efficiency.
Singularity avoidance: pass through singular points slowly
- Mathematical expression: The singular pose of the robot arm implies that the Jacobian matrix is no longer full rank.
- Algorithmic behavior: The existence of infinite solutions leads to attempts to achieve large instantaneous rotations for J4 and J6.
- Solution: Detect the position of singular points in advance, limit joint speeds, and pass through the singular point-related area slowly.
Controller hardware enhancement
NexDroid 2.0 comes with the new controllers C1200 and C1201. The CPU has been upgraded from J1900 to J6412, resulting in a 3x improvement in overall computational performance. It now supports up to 64 axes of simultaneous motion, compared to the previous 24 axes. The multi-port design simplifies the wiring in industrial settings, replacing the previous industrial switch solution by unifying the interfaces for devices such as cameras and PLCs. The inclusion of a supercapacitor UPS module effectively addresses hardware damage and data loss caused by unauthorized power outages in industrial scenarios. It also provides data recovery functionality, allowing the resumption of operation logic prior to the power outage to ensure continuous production on-site. C1201 is also equipped with versatile peripheral interfaces, featuring an X86+FPGA structure to ensure high-speed IO output. Furthermore, the configuration of PWM/CAN interfaces enables C1201 to be applied in more complex process scenarios such as laser welding and cutting.
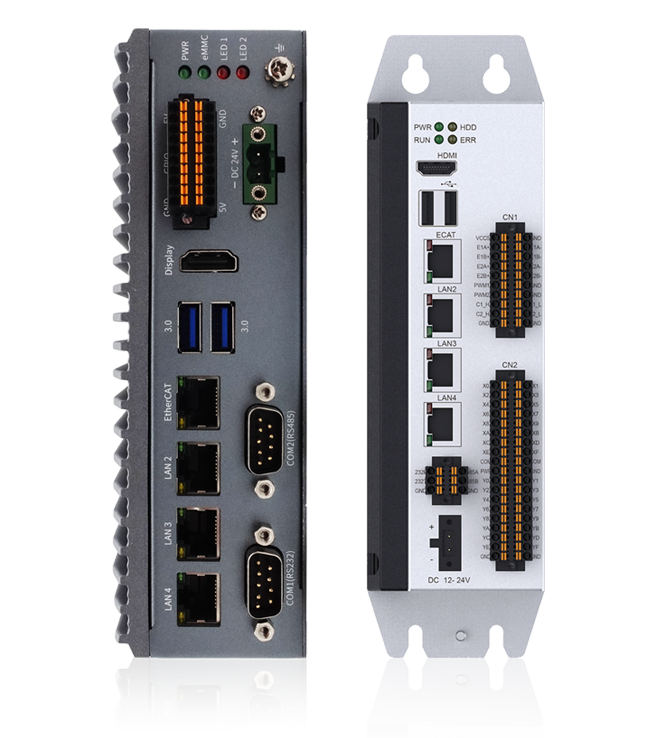
Drive and control integrated cabinet 2.0
It provides multiple interfaces such as EtherNet, RS485/232, and EXTENC, along with a built-in IO module that offers 16 outputs and 24 inputs for convenient customization by customers. Single-axis rated current can reach 9A. Despite its compact size, it possesses great energy and can drive motors up to 1.5kW, supporting various leading motor brands. Modular design ensures easy maintenance, upgrades, and expansions. Optimized volume: reduced by 21% compared to the previous generation, with a total weight of only 7kg. Board connections minimize internal cabinet cable count from 30 to 10, enhancing stability. With just one Ethernet cable, robot and servo debugging can be completed, increasing efficiency.
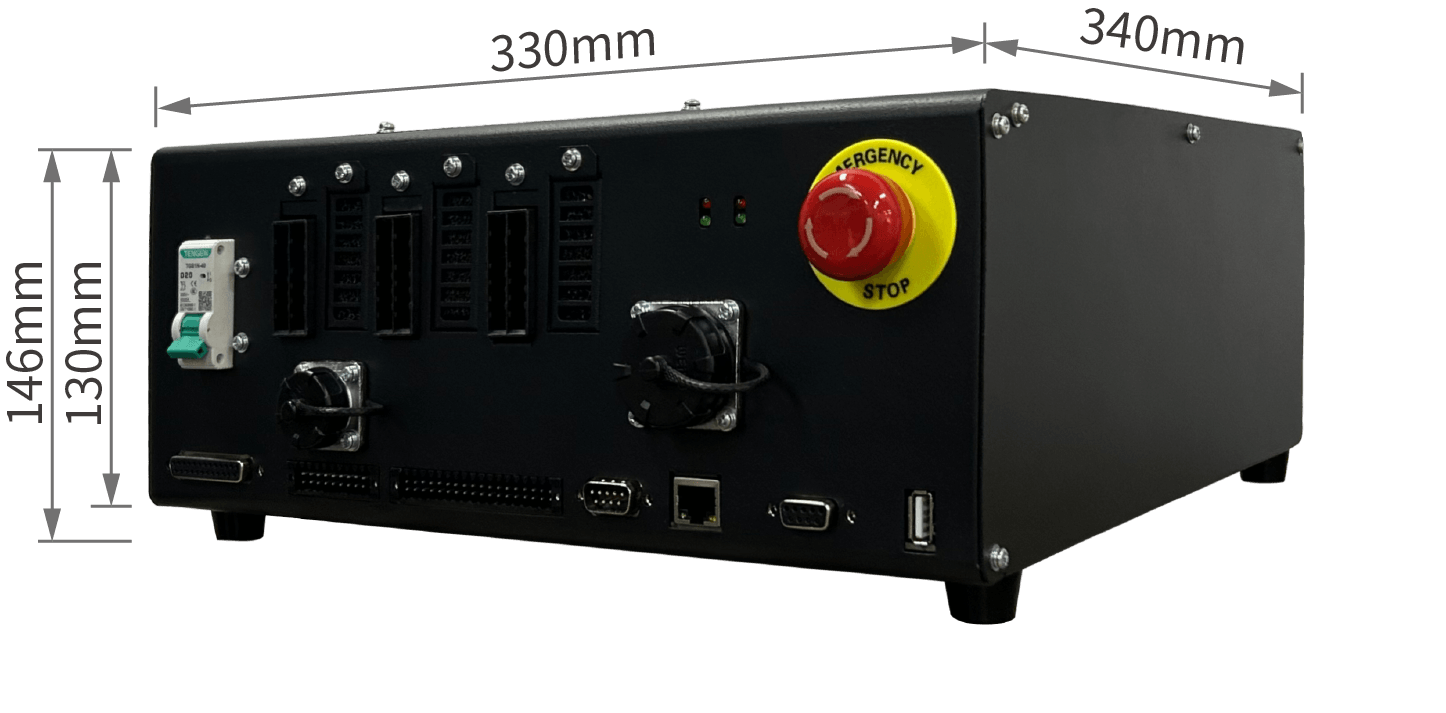
Star-1 collaborative control cabinet
Built-in 48V power supply output (1500W power) Compliant with safety regulations Standard aviation plug Supports EtherCAT expansion axis Supports TCP/IP IP65 waterproof
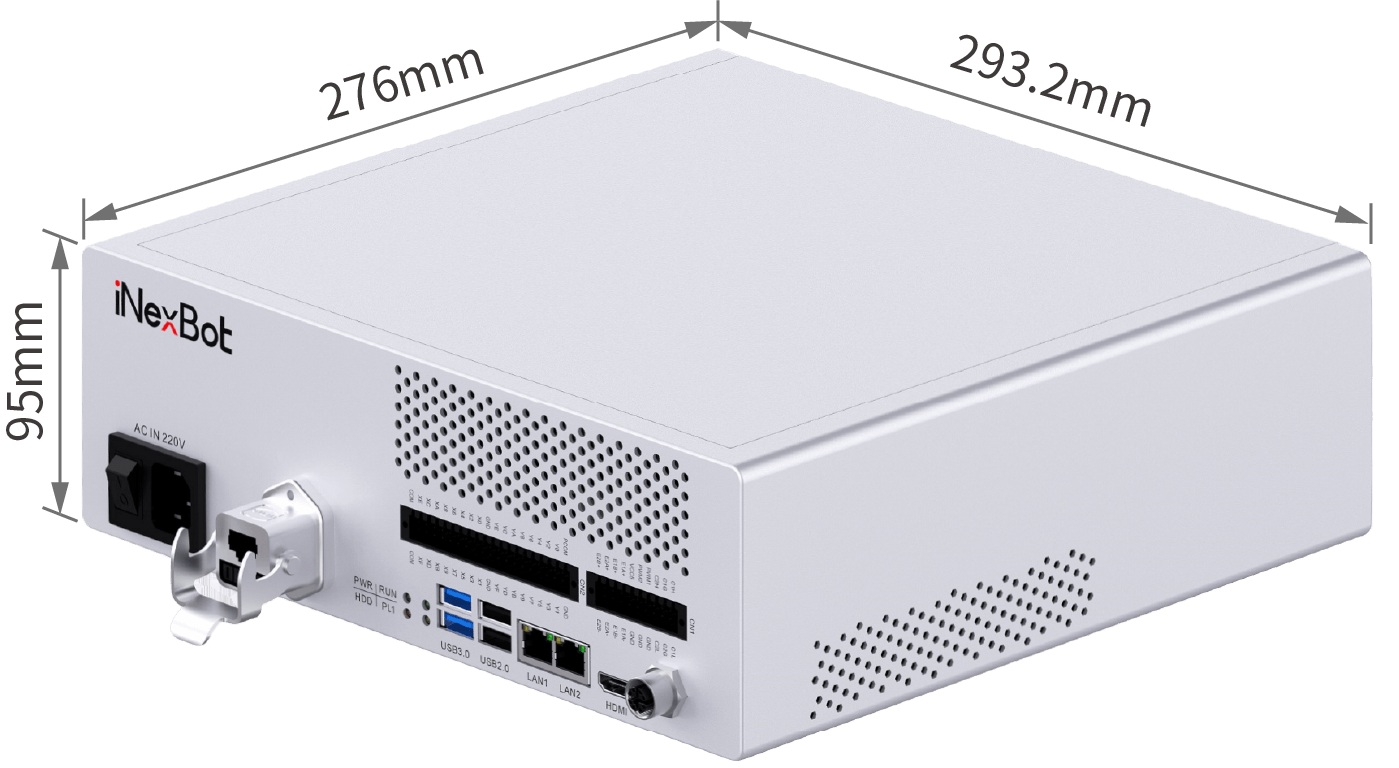
Process improvement
Perfect multi-layer multi-pass welding
Supports custom trajectory offset, indentation, push angle, tilt angle, etc., and also enables adaptive tracking
One-to-many welding
Up to four welding machines can be connected simultaneously.
Flying shooting process
- Eye on hand: The camera is mounted on a tool hand for flying positioning.
- Eye off hand: The camera is fixed on the moving path of the object being tested for high-speed flying positioning.
- The positioning accuracy can reach within 0.2mm.
Conveyor belt tracking technology
- Utilizes dynamic tracking and synchronization algorithm: Dynamic synchronization suitable for high-speed and high-precision synchronization scenarios.
- One-to-many: One robot can intelligently handle multiple conveyor belts, improving efficiency.
- Multi-robot collaboration: Multiple robots collaborate for high-speed and dynamic sorting. Mainly applied in industries such as food and pharmaceuticals for quick sorting and packaging, resulting in higher efficiency.
- Multi-tool switching: During tracking, the robot can freely switch between different tools and simultaneously grip multiple targets.
Vision and control integrated technology
Integrate vision software into control systems.